Caitlin Chin
Project 2A - Individual Advanced Construction Tectonic and Material Study
Project 2A - Individual Advanced Construction Tectonic and Material Study
This assignment objective is to develop a deep understanding of the concept of Architecture as current and future artistic expression of tectonic materiality in an advanced constructed building, in a geographically relevant place. Students will look at the system of elements, techniques and technologies, current and as forecast and their affect on the practice of Architecture, the construction industry and sustainable futures. In addition, the project goal is to provide applied construction techniques and manufacturing in order to prepare the student for future professional engagement.
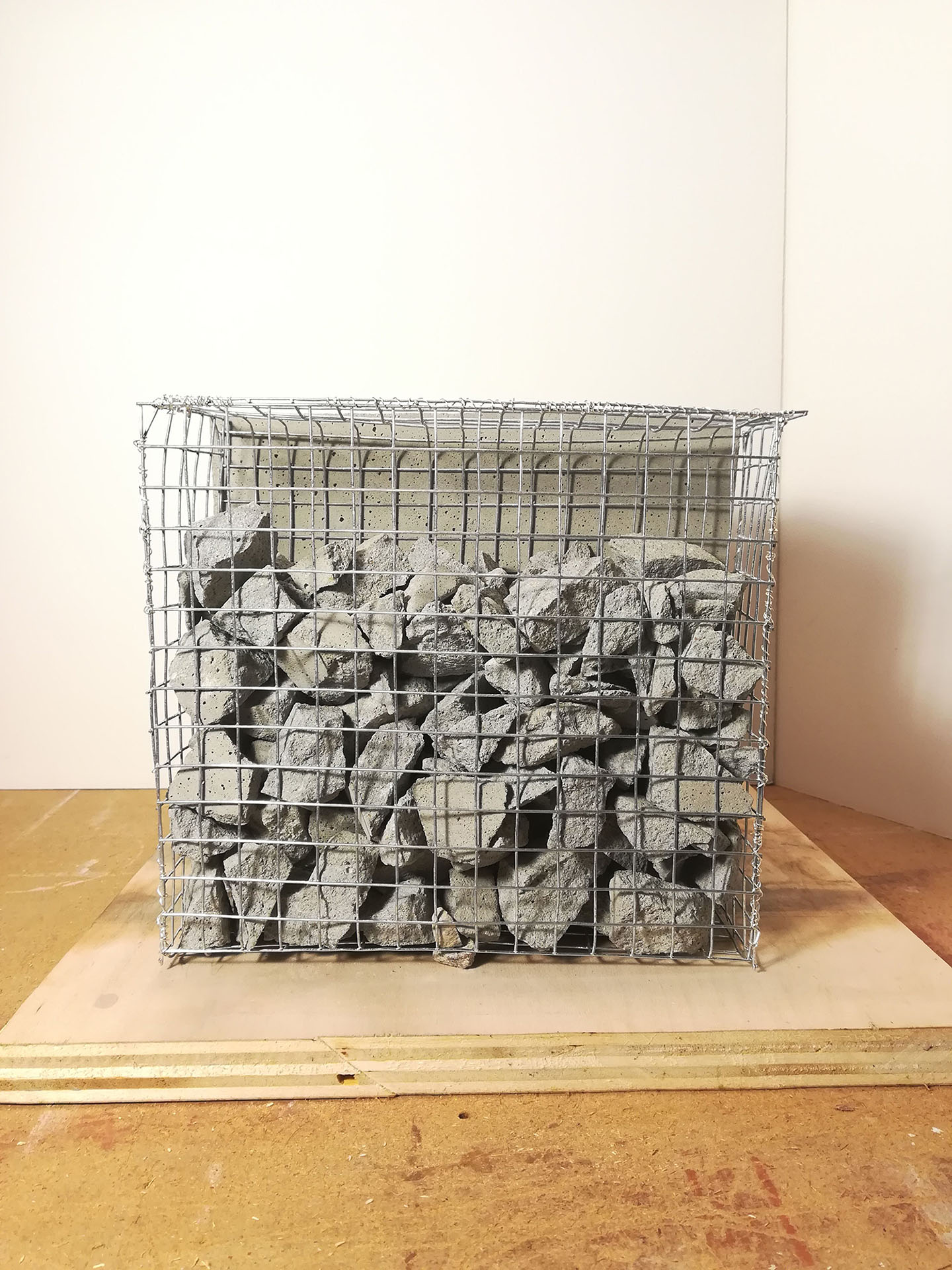
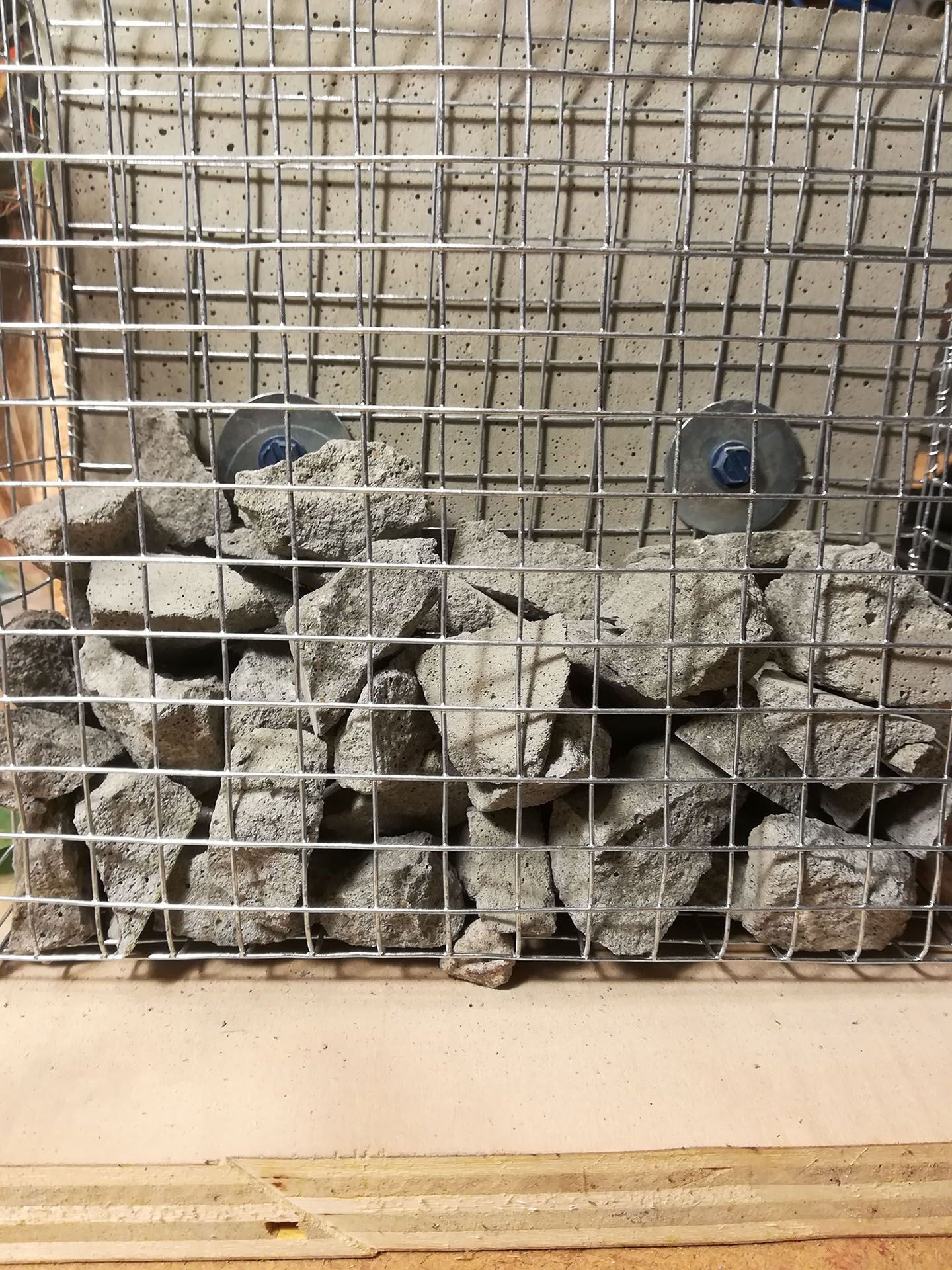
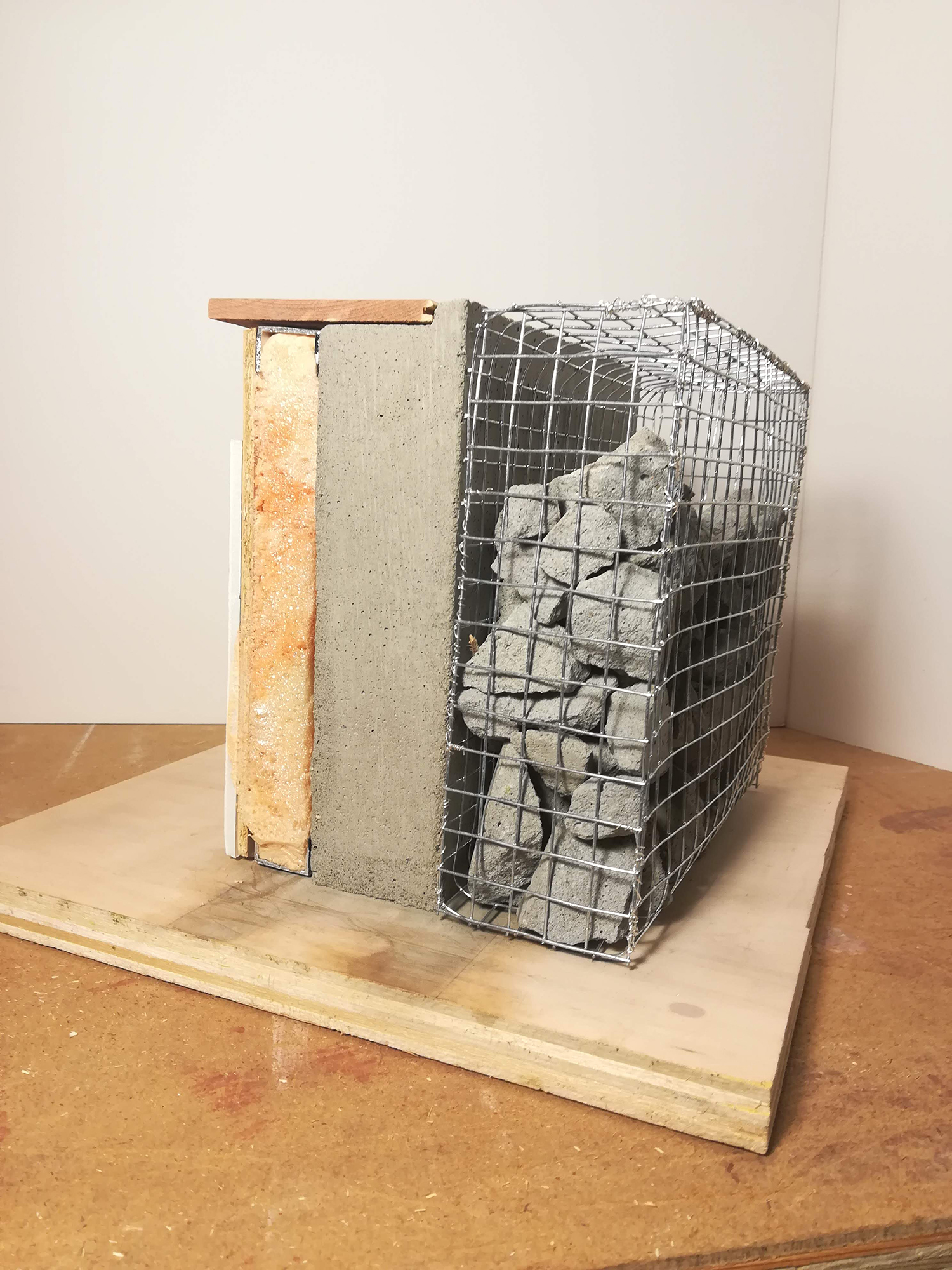

This building is a concrete building through and through. The main structure is made of reinforced concrete and the gabion cage is the exterior cladding. These gabion walls are filled with ballasts that is crushed concrete instead of stone which speaks their intention of recycling concrete. Because the gabion cage still allows rain and snow to interact directly with the structural wall, there is a sealant applied to the exterior side of the wall. Next will be the insulation, plywood and gypsum layers used for the interior finish of the wall. Douglas fir wood was also used as an accent material in this detail for the interior window frame. Their wood accents speak to their intention to reconnect with nature and their sustainable approach to concrete as the building is right beside Mt. Sobaek National Park.
How it relates to the Overall Conception:
The Hanil cement plant, the client of the Hanil Visitor Centre & Guest House, acknowledges the environmental impact of concrete as a problem. The intention of the visitor centre and guest house is to educate visitors about recycled concrete. The building itself showcases the potential of recycled concrete through different types of formwork and casting techniques in its own construction. As mentioned before the ballasts used for the gabion wall was crushed, leftover concrete of the east wall which supports their goal into looking at new ways of recycling concrete. This introduces the concept of a closed loop construction process between the waste of the east wall to be reused in the south wall. The crushed concrete was also used for the roof, interior railings in gabion cages and larger ballasts were integrated into the landscape design. The future for this interpretation of the gabion wall provides opportunity of using recycled concrete ballasts without worrying about the structural integrity of the concrete.
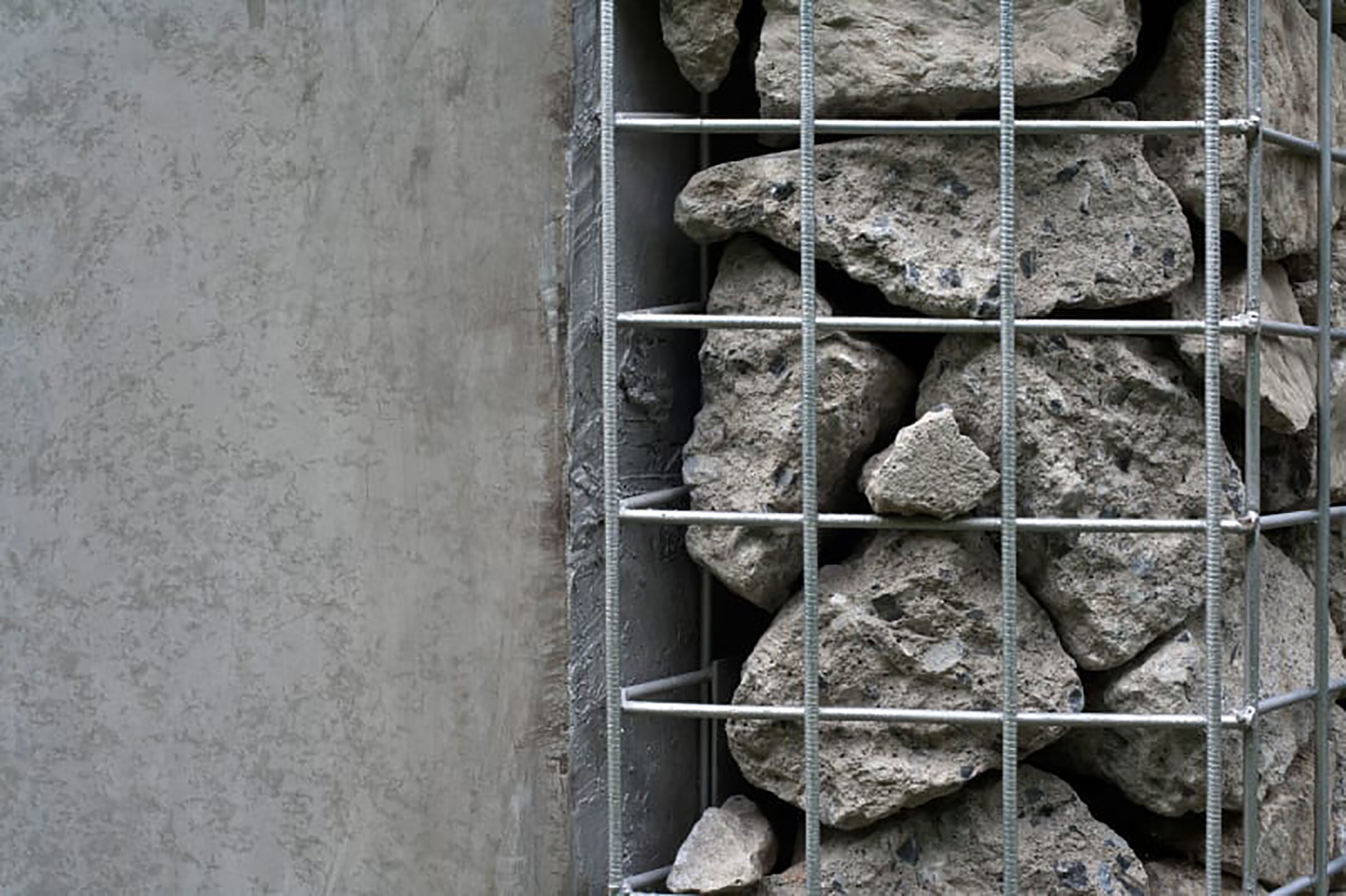
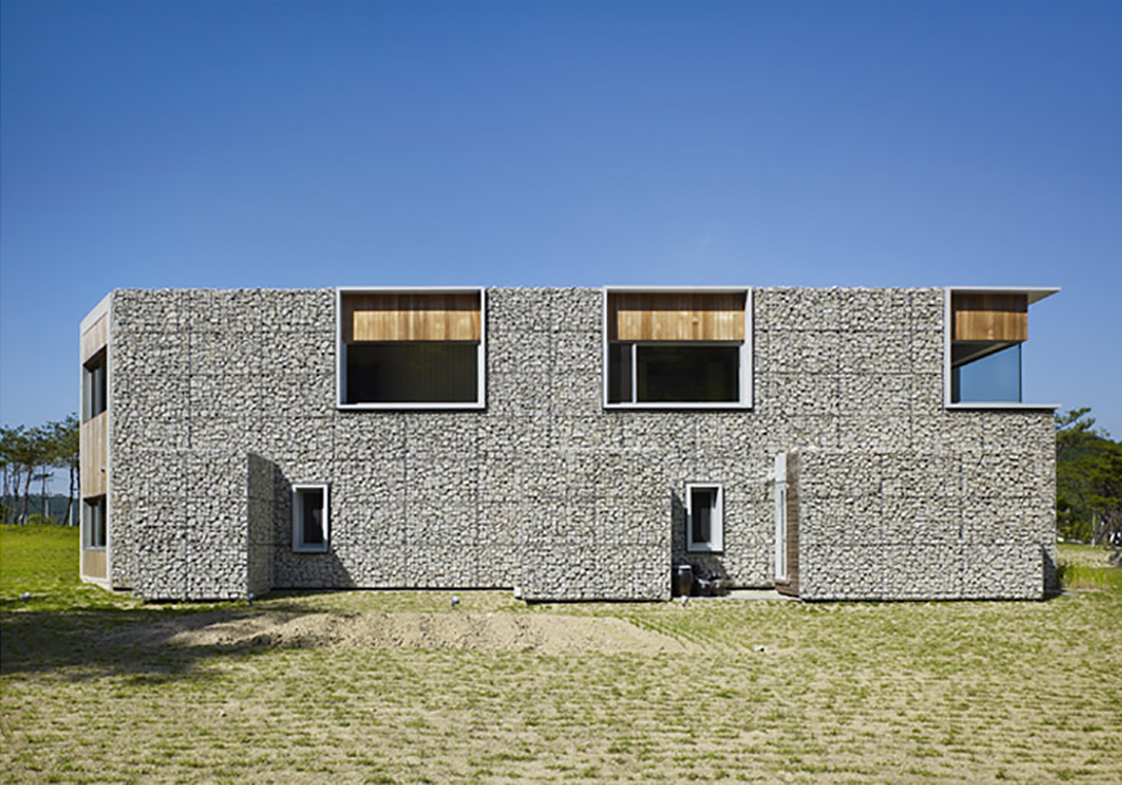
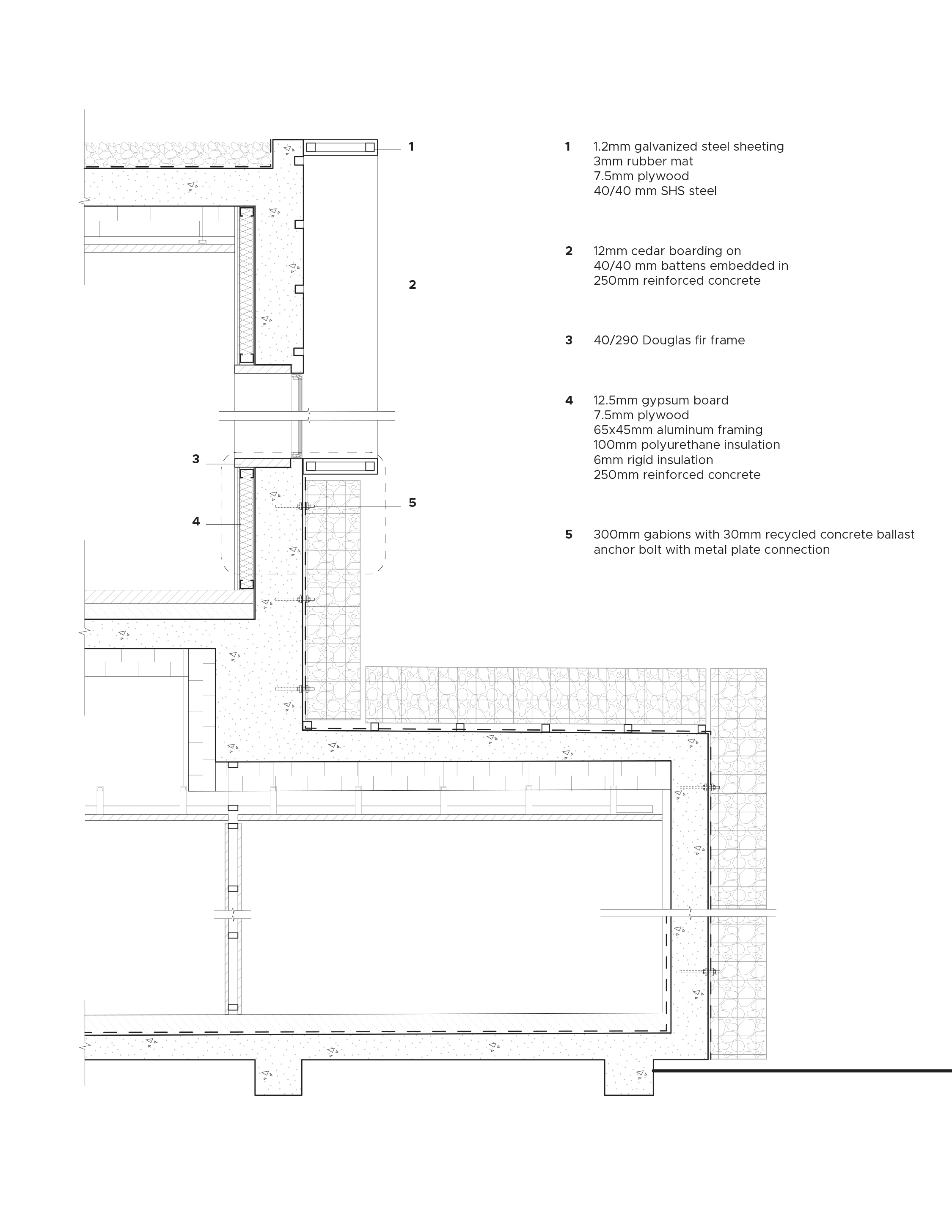
Why the Detail was Chosen:
The chosen detail is the south gabion wall of the Hanil Visitor Centre & Guest House in Korea. This wall acts as one of the main facades of the building along with the east fabric formed wall. The construction of the wall is significant because it reinterprets the typical use of a gabion wall. Traditionally, gabion walls are filled with stone and used as a retaining wall, but in this project the leftover concrete from the east wall was crushed to take the place of the stone. Therefore, the gabion wall acts more as a cladding element that is attached to the reinforced concrete wall behind it.
Caitlin Chin
Project 2B - Tectonic and Material Design, Innovation, and Entrepreneurship
Project 2B - Tectonic and Material Design, Innovation, and Entrepreneurship
The assignment objective is to develop in the students the primary ingredients of design, innovation and entrepreneurship required for the architectural and construction industries. The professional scope of the Architect is changing dramatically in the 21st century. In the future, Architect’s ideas will permeate the fabrication process in its entirety. A new relationship is being established between the Architect’s traditional responses towards advanced construction in terms of tectonics and materiality.
The Hanil Visitor Centre and Guest House
Location: 77, Pyeong-ri, Maepo-eup, Danyang-gun, Chungbuk, Korea
Architect: Byoung-soo Cho (BCHO Architects)
Client: Hanil Cement Plant
![]()
Refabrication: New Material Concept
The Hanil cement plant, the client of the Hanil Visitor Centre & Guest House, acknowledges the environmental impact of concrete as a problem. Within the visitor and guest house contains samples of different ways the Hanil Cement Plant has been experimenting with various methods of using concrete. They have the intention of coming up with new ways to use concrete in non-typical ways and combining it with other materials and methods. The south wall currently has the exterior cladding as a gabion cage wall that uses recycled concrete as ballasts. However, the construction currently in place has the cage connected flat against the solid surface of the structural reinforced concrete wall. The program of the ground floor can benefit from natural daylight. The specific detail is of the electrical room that is indicated on the plan. So instead of the gabion cage, the translucent tile that the center has been experimenting with can be an alternate cladding material to allow light to enter the interior space and to display another method of recycling concrete on the building. Also in the current detail there is no interior or exterior insulation for this space, which allows for some material experimentation.
The material alternative is an option seen on the right. The tile has the crushed concrete and then resin is poured over the ballasts. The amount of concrete within the tile and the pattern that the concrete pieces can make is all customizable. As seen on the examples on display, some tiles have the concrete emerging from the resin while in others the concrete is fully submerged. It can also have different finish qualities to the surface. It can be glossy or matte.
Location: 77, Pyeong-ri, Maepo-eup, Danyang-gun, Chungbuk, Korea
Architect: Byoung-soo Cho (BCHO Architects)
Client: Hanil Cement Plant
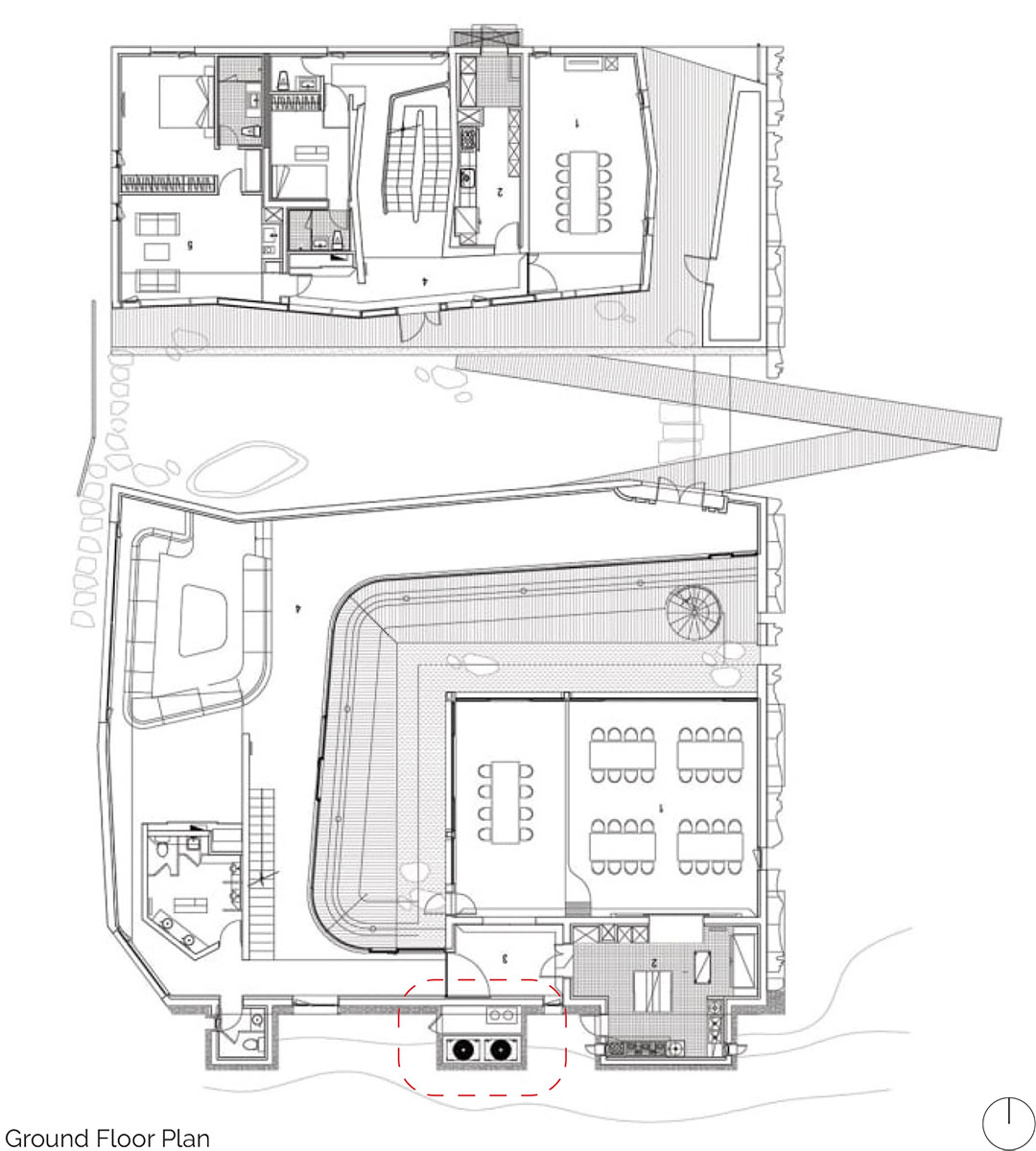
Refabrication: New Material Concept
The Hanil cement plant, the client of the Hanil Visitor Centre & Guest House, acknowledges the environmental impact of concrete as a problem. Within the visitor and guest house contains samples of different ways the Hanil Cement Plant has been experimenting with various methods of using concrete. They have the intention of coming up with new ways to use concrete in non-typical ways and combining it with other materials and methods. The south wall currently has the exterior cladding as a gabion cage wall that uses recycled concrete as ballasts. However, the construction currently in place has the cage connected flat against the solid surface of the structural reinforced concrete wall. The program of the ground floor can benefit from natural daylight. The specific detail is of the electrical room that is indicated on the plan. So instead of the gabion cage, the translucent tile that the center has been experimenting with can be an alternate cladding material to allow light to enter the interior space and to display another method of recycling concrete on the building. Also in the current detail there is no interior or exterior insulation for this space, which allows for some material experimentation.
The material alternative is an option seen on the right. The tile has the crushed concrete and then resin is poured over the ballasts. The amount of concrete within the tile and the pattern that the concrete pieces can make is all customizable. As seen on the examples on display, some tiles have the concrete emerging from the resin while in others the concrete is fully submerged. It can also have different finish qualities to the surface. It can be glossy or matte.
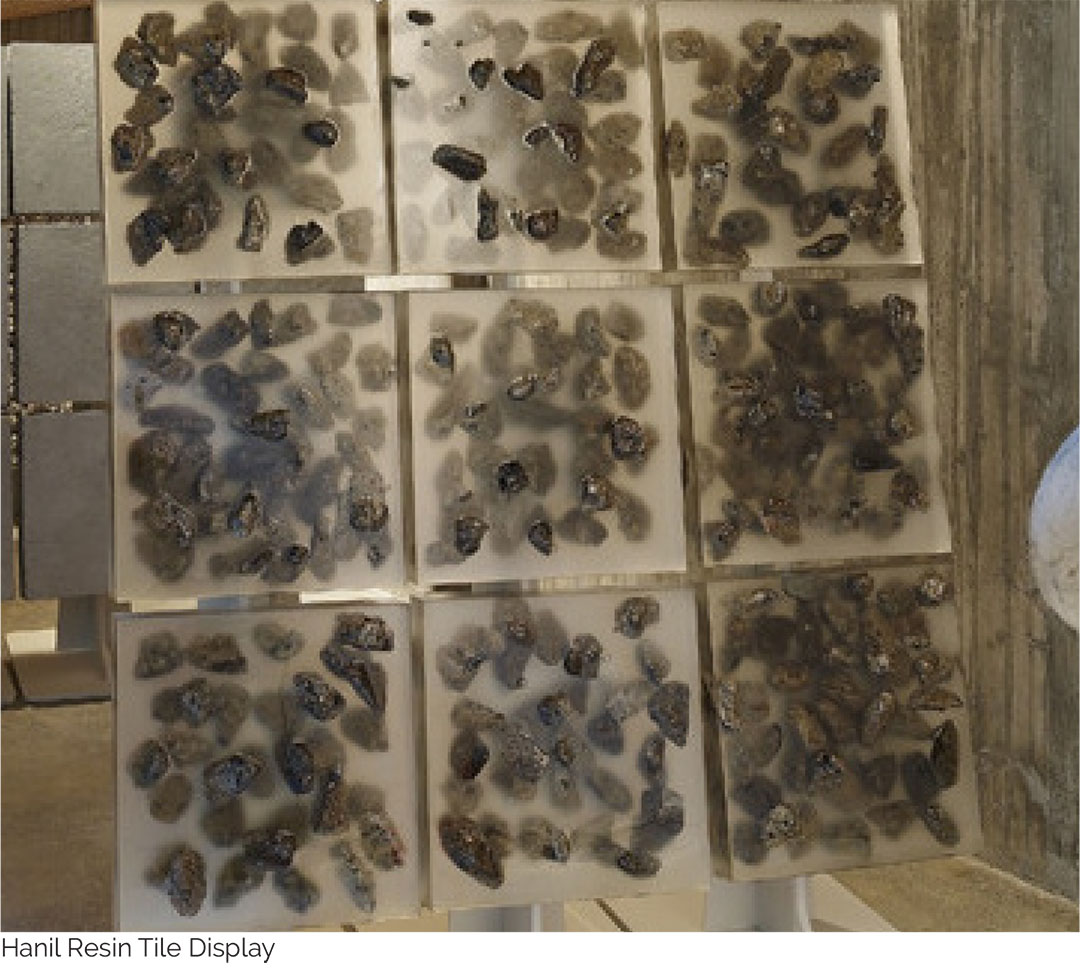
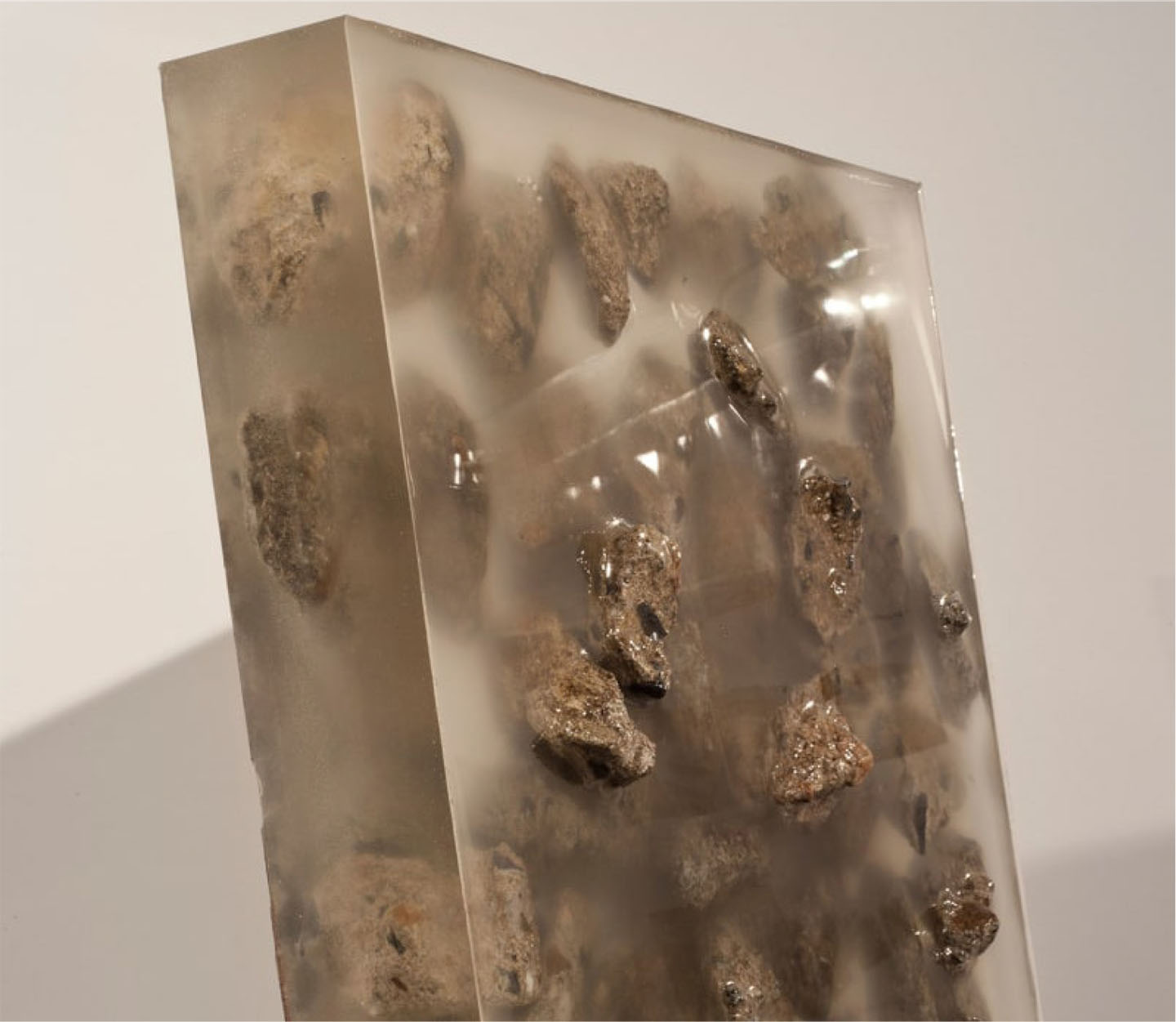
Resin Material Properties:
Casting resin is specifically designed to be casted into molds, forms, and figures. The two components of casting resin that makes it an interesting material is the low-viscosity and the ability to harden over time. Because of these properties casting resin can be used for projects that require a thicker application/ depth. Casting resin differs from epoxy resin. Epoxy resin is more viscous, has a faster curing time but can only be applied to projects with a maximum depth of 2cm (Resin Expert, 2020).
Looking into specific products for casting resin is a thermosetting resin, specifically made from polyethylene terephthalate. It is highly transparent and stiff, and it has excellent gas barrier properties. Some example of products that are made from this material is insulation, and high-performance optical films (Daido Chemical Corporation).
When in the process of casting, formwork needs to be considered. It is recommended to use silicone molds to allow for a smooth finish but also allows for easy removal of the mold. The first step would be to have a thin layer of resin in the mold to begin with and then to add the desired amount and pattern of the recycled concrete pieces. Next, additional casting resin will be poured over concrete pieces and to reach the desired thickness. It is recommended to dry for 24 hours but it also varies based on the thickness of the piece casted.
I am looking at the thin resin tiles that the Hanil Cement Plant has experimented with and making it into something that is thicker, and block like. I will be looking at glass blocks and their construction methods of wall construction for the proposed resin blocks.
Glass Block History:
The invention of glass has made a huge impact on the building industry as it allows natural daylight and views to be accessible from the interior of the building. The use of glass blocks has been reinvented over the years as it has varied in use as an interior or exterior element in the form of walls, ceilings, and floors. Glass blocks have been important in the interior architectural design to illuminate adjacent rooms and hallways mainly. The glass can be manufactured to provide the desired degree of visibility to allow for privacy and light permeability. In the exterior context, glass blocks maximize natural light to reduce energy required for artificial lighting (Architectural Products and Services, 2018).
In 1907, Deutsche Luxfer-Prismen-Gesellschaft patented the glass block strengthening process where the two pieces of glass are joined but the centre is hollow. The “air gap” within enhances the insulating qualities that glass blocks and helps with sound deadening, and fireproofing. In present day context, the pattern, texture degree of transparency and size can all be customized for any project. Additionally, over the years different mortars and silicones have been improving to join the glass blocks together (Architectural Products and Services, 2018).
I am hoping to explore and treat the resin concrete blocks similarly to the glass block construction. I will be referring to different modern examples that used glass blocks in an innovative way and looking at different details that I can learn from for the resin concrete blocks.
![]()
The invention of glass has made a huge impact on the building industry as it allows natural daylight and views to be accessible from the interior of the building. The use of glass blocks has been reinvented over the years as it has varied in use as an interior or exterior element in the form of walls, ceilings, and floors. Glass blocks have been important in the interior architectural design to illuminate adjacent rooms and hallways mainly. The glass can be manufactured to provide the desired degree of visibility to allow for privacy and light permeability. In the exterior context, glass blocks maximize natural light to reduce energy required for artificial lighting (Architectural Products and Services, 2018).
In 1907, Deutsche Luxfer-Prismen-Gesellschaft patented the glass block strengthening process where the two pieces of glass are joined but the centre is hollow. The “air gap” within enhances the insulating qualities that glass blocks and helps with sound deadening, and fireproofing. In present day context, the pattern, texture degree of transparency and size can all be customized for any project. Additionally, over the years different mortars and silicones have been improving to join the glass blocks together (Architectural Products and Services, 2018).
I am hoping to explore and treat the resin concrete blocks similarly to the glass block construction. I will be referring to different modern examples that used glass blocks in an innovative way and looking at different details that I can learn from for the resin concrete blocks.
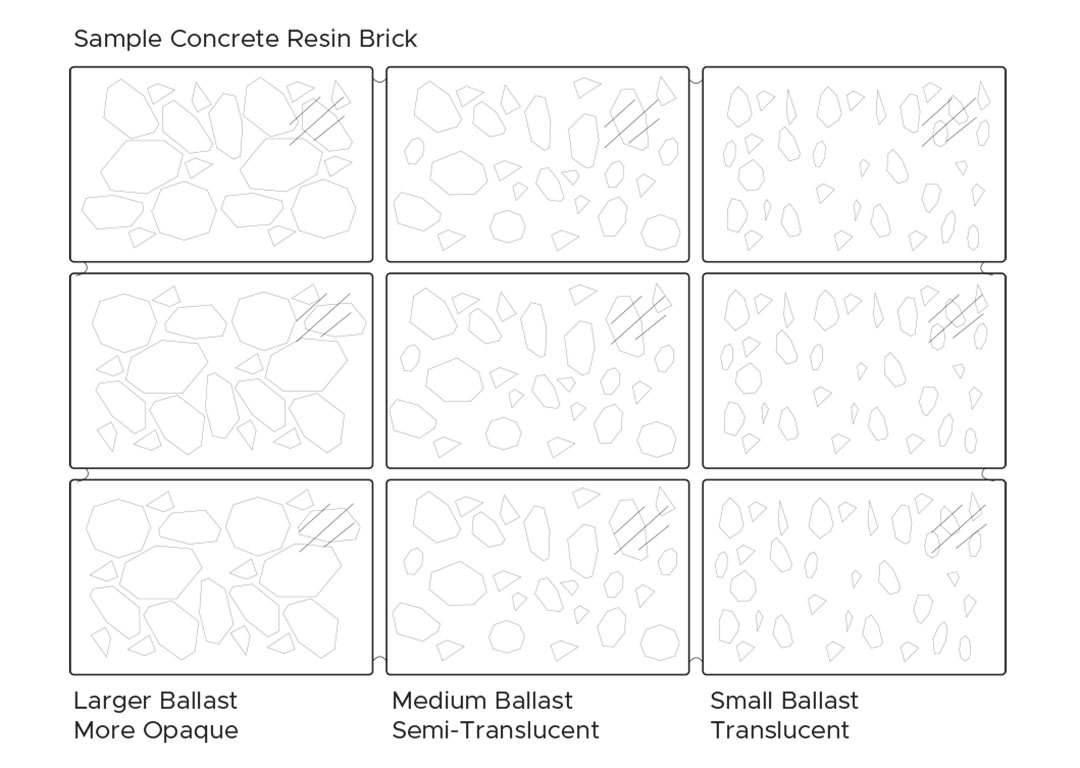

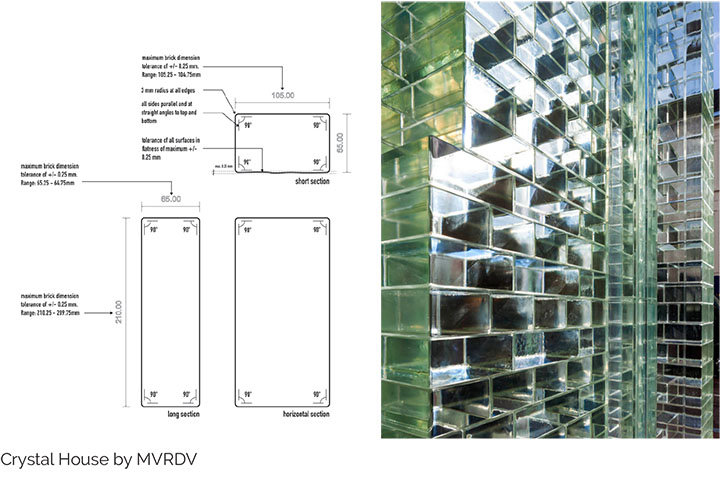
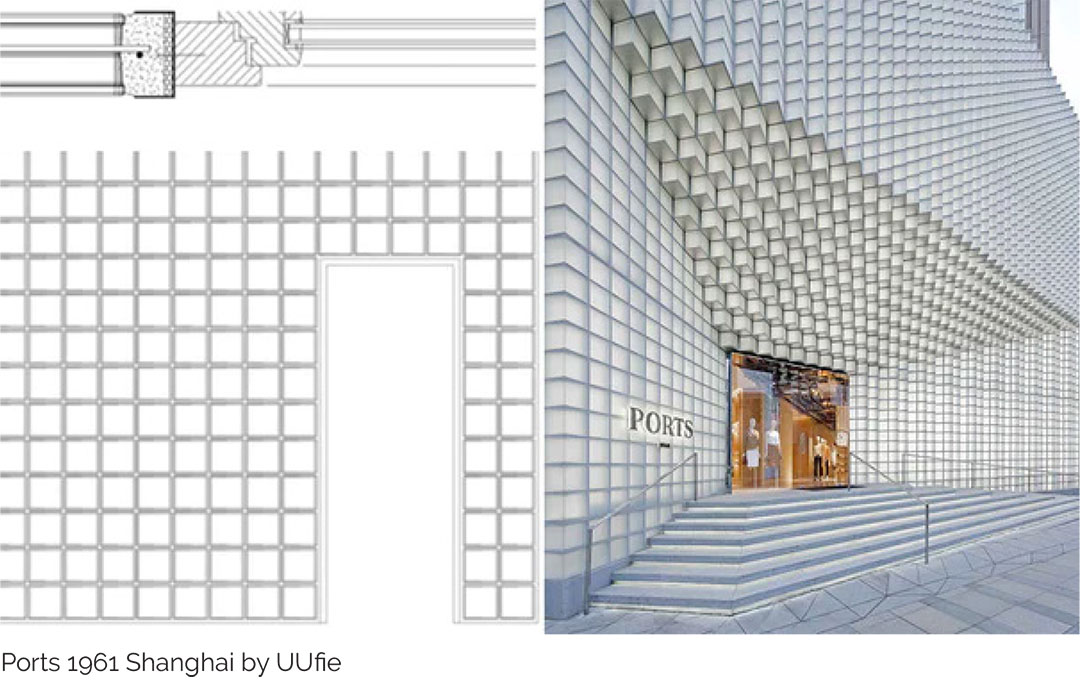
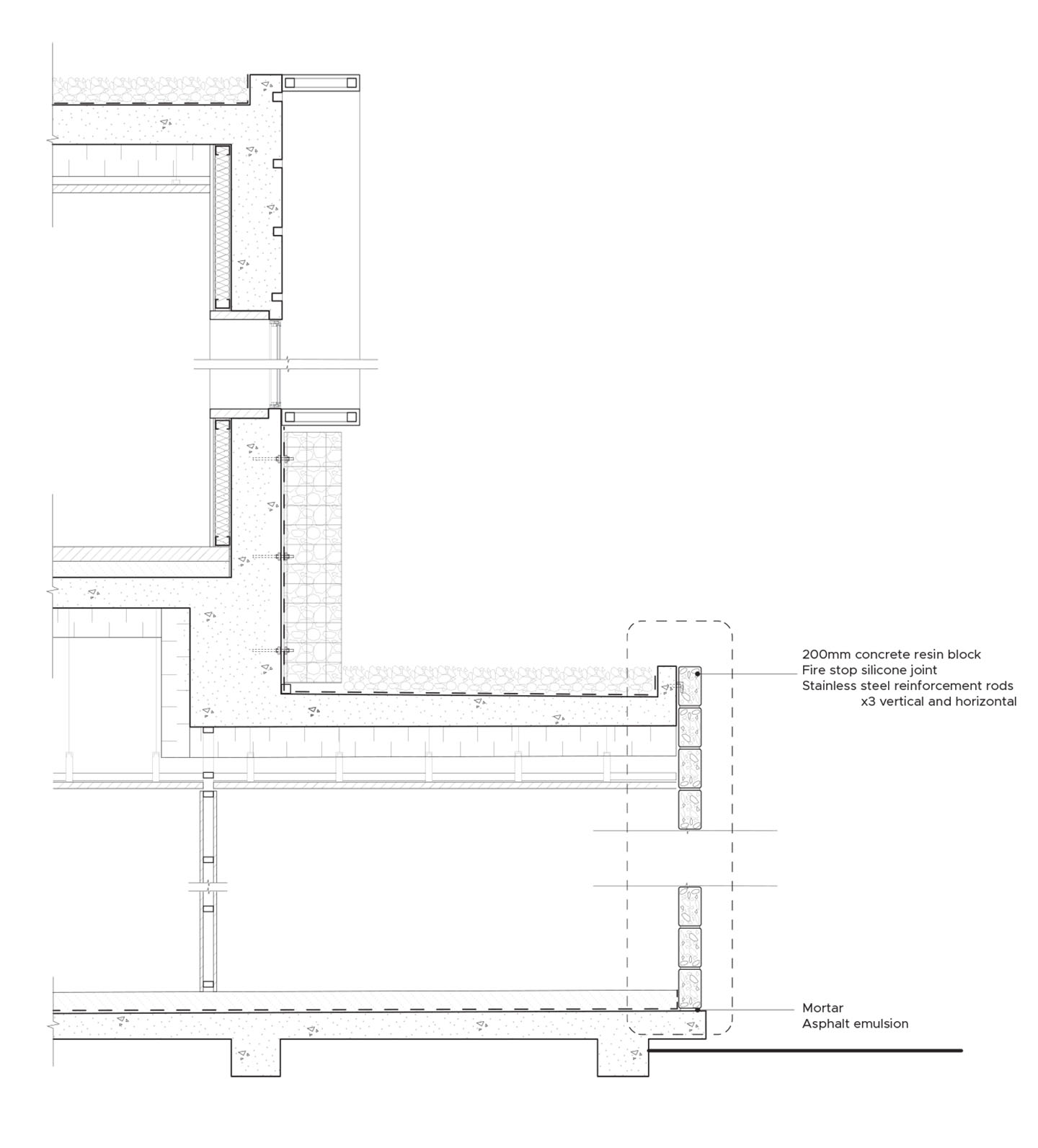
Chanel Wase
Project 2A - Individual Advanced Construction Tectonic and Material Study
Project 2A - Individual Advanced Construction Tectonic and Material Study
SANAA New Contemporary Art Museum
This assignment objective is to develop a deep understanding of the concept of Architecture as current and future artistic expression of tectonic materiality in an advanced constructed building, in a geographically relevant place. Students will look at the system of elements, techniques and technologies, current and as forecast and their affect on the practice of Architecture, the construction industry and sustainable futures. In addition, the project goal is to provide applied construction techniques and manufacturing in order to prepare the student for future professional engagement.
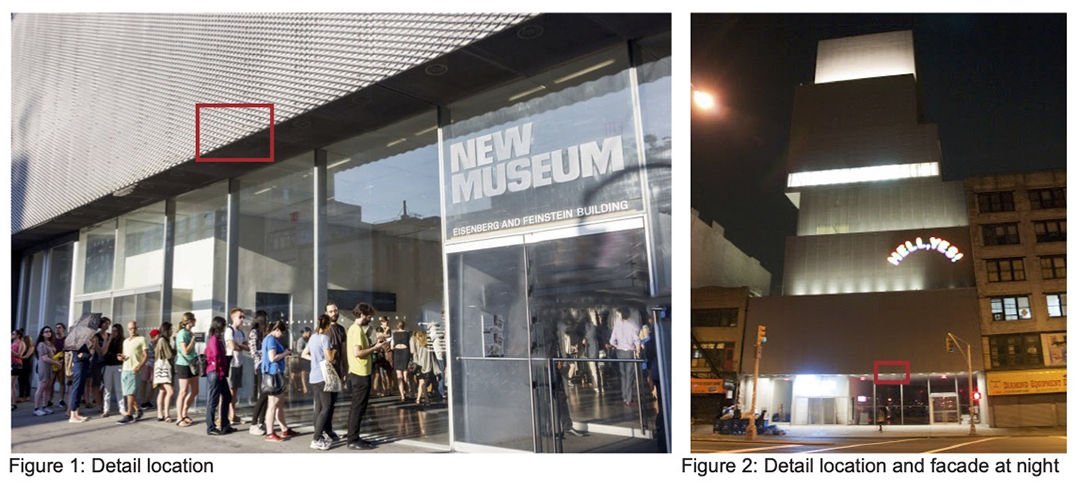
The detail being studied is taken from the overhang at the entrance of The New Art Museum by SANAA architects (Figure 1). The concept behind the building was to create shifting boxes which fit in and reflect the New York cityscape where it is located. From a distance, the building is seen to be clean and monochrome, and fits in well with the cityscape, but upon closer inspection, it is made up of a more industrial continuous mesh facade. This can be seen as a metaphor for the New York cityscape in general.
The building’s facade is made up of an anodized expanded aluminium mesh bolted directly to aluminum panelled walls (Figure 4). Aluminum was chosen due to its light weight and cost efficiency. This aluminum mesh skin wraps the entire building, softening its edges and hiding the windows throughout the day. This was meant to allow the building to melt into its surroundings and increase its sense of transparency and lightness. The mesh panels themselves are made to a standard size to reduce costs, each 4’ long with 6 diamond shapes of width. The separate panels are overlapped at the centre of the diamond shape to hide the joints and allow for the appearance of a continuous wall. The clips which attach the aluminum mesh to the interior aluminum panels are steel, which may cause problems in the future due to being a different metal. However, they are strong supports, and are made at an angle in relation to the angled diamond shapes of the mesh panels, which allows them to remain hidden out of view, also contributing to the continuous look of the facade.
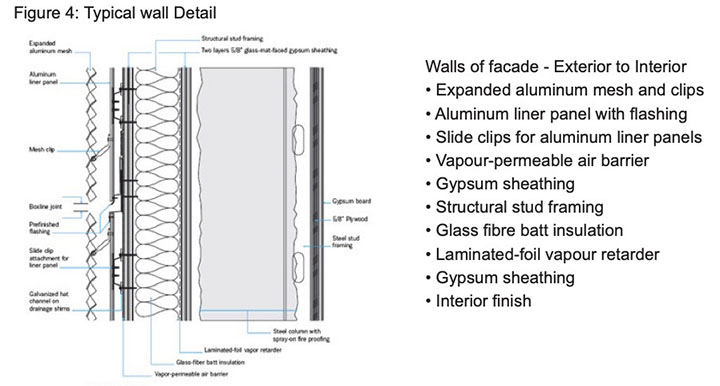
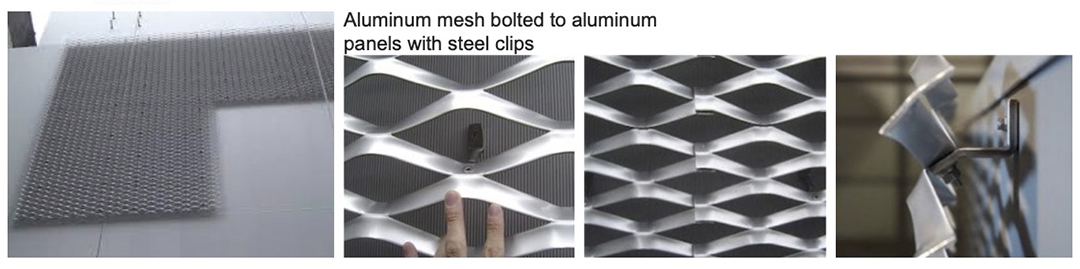
The expanded aluminium mesh on the facade is a material usually used for fencing, but SANAA was able to demonstrate a new way to use this material as a continuous skin for a building. Their research into this detail is not yet perfect, as the joints at the corner of the building are not continuous, and they are criticized for the interior look of the mesh through the windows. However, this use of aluminum mesh may be, and has been, re-fabricated and customized into other similar building facades. It is a good precedent to see how a non-traditional material can be used for aesthetic and building purposes as a skin on a facade.
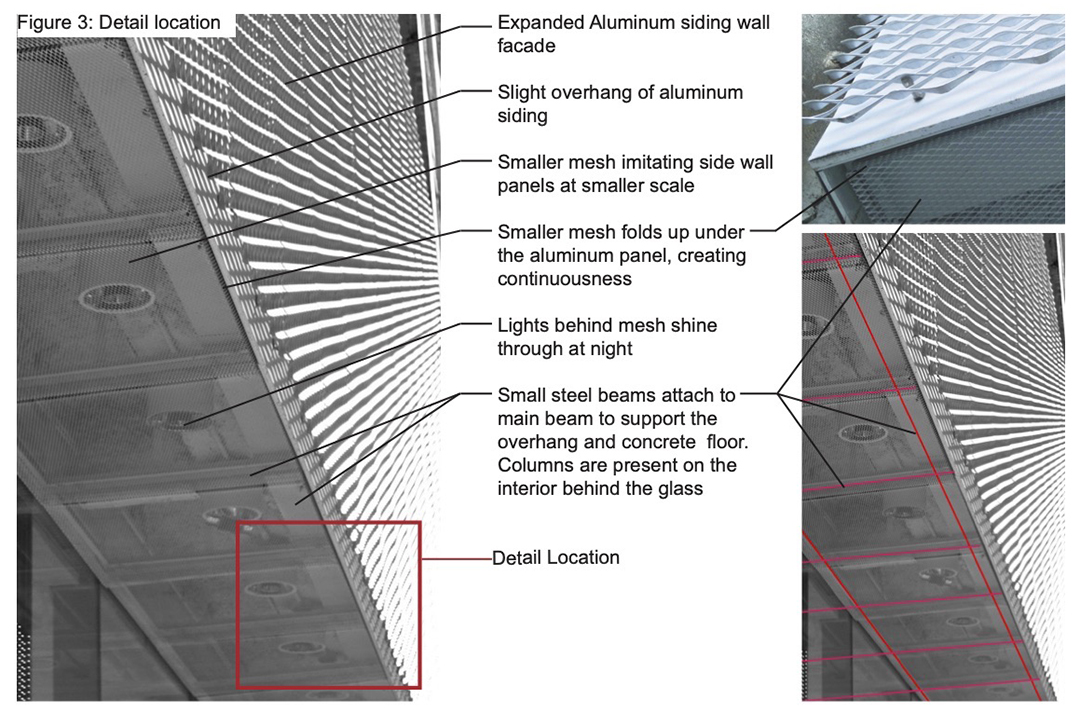
In order to demonstrate transparency to the outside world, the main entrance of the New Art Museum has a large glass wall, and continues the exterior concrete sidewalk into the interior (Figure 1). This entrance includes a small overhang of the building above. Unlike other overhangs present in the building, which simply use white panels to close off the overhang’s bottom, this one is more visible to passerby, and is more detailed to accommodate this. The bottom of the overhang is covered by a small metal mesh which turns up to seamlessly hide behind where the aluminum mesh panels of the wall’s facade hang down (Figure 3). The use of a mesh below the overhang allows for the continuous feeling of the building’s facade to remain unbroken to people walking under.
This overhang mesh detail also imitates the building’s interior skylights, which are one of the main natural light sources inside of the building, created in the spaces between the shifting box shapes. By putting lights behind the overhang’s mesh where the structure is, the overhang shines down light at night, just like the actual skylights which shine in the interior (Figure 2). This also enforces the concept of transparency and connection between interior and exterior.
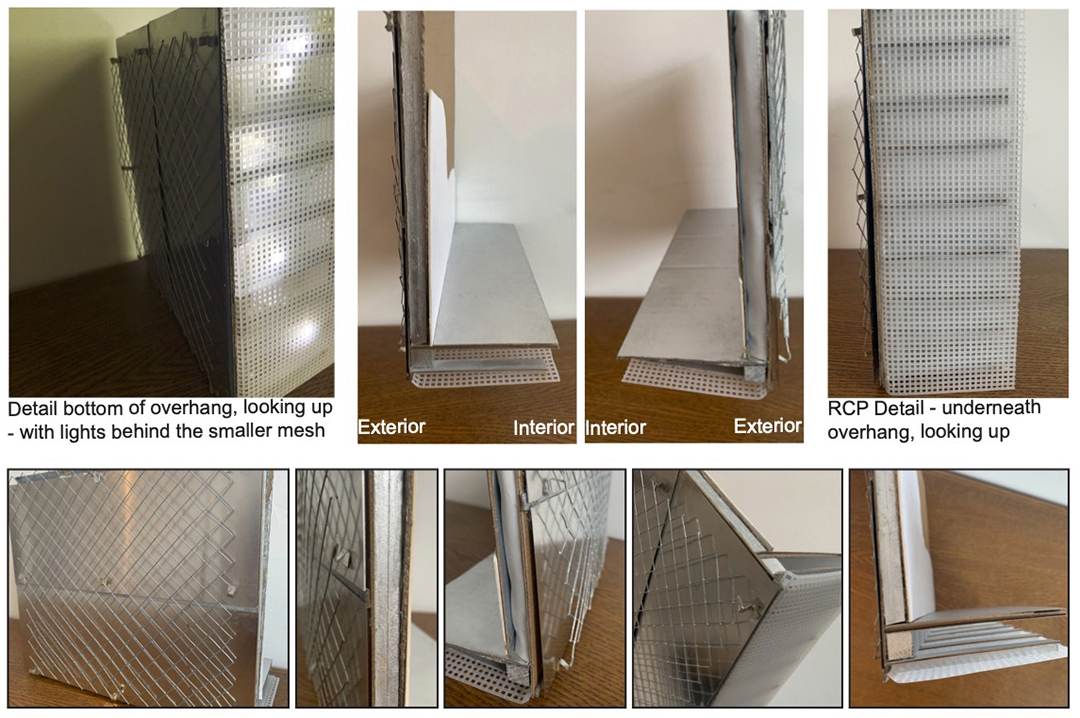
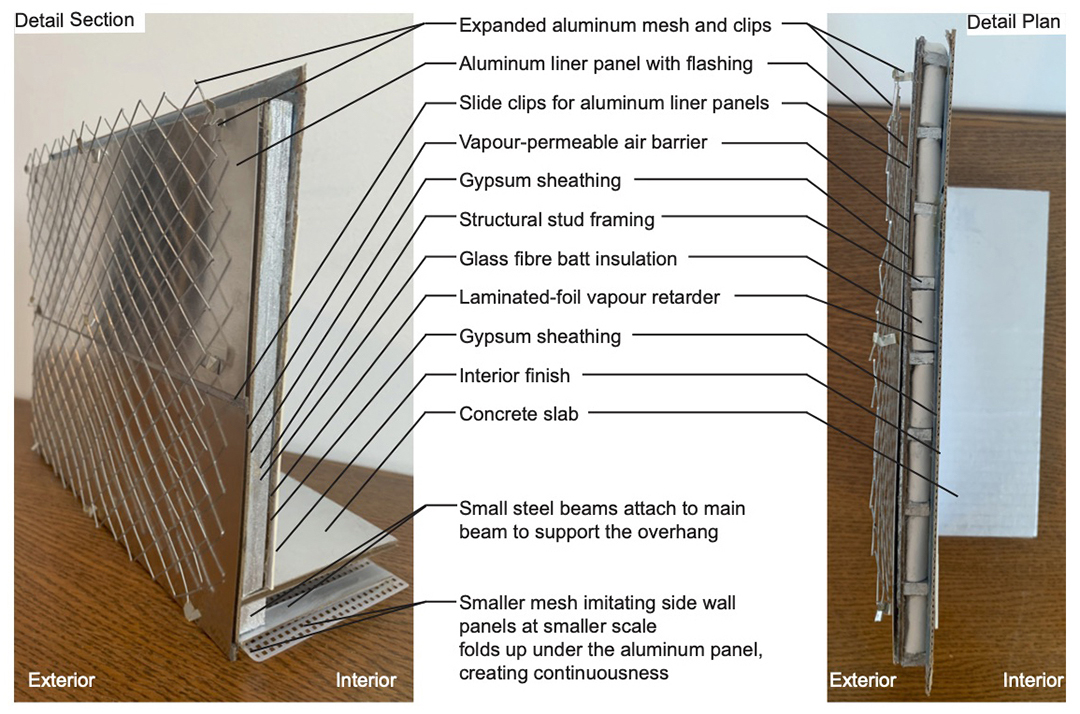
Chanel Wase
Project 2B - Tectonic and Material Design, Innovation, and Entrepreneurship
Project 2B - Tectonic and Material Design, Innovation, and Entrepreneurship
Metal Mesh Facade
The assignment objective is to develop in the students the primary ingredients of design, innovation and entrepreneurship required for the architectural and construction industries. The professional scope of the Architect is changing dramatically in the 21st century. In the future, Architect’s ideas will permeate the fabrication process in its entirety. A new relationship is being established between the Architect’s traditional responses towards advanced construction in terms of tectonics and materiality.
The facade detail of the New Art Museum by SANAA architects has been greatly studied for the completion of this assignment. The concept behind the building was to create shifting boxes which fit in and reflect the New York cityscape where it is located. From a distance, the building is seen to be clean and monochrome, and fits in well with the cityscape, but upon closer inspection, it is made up of a more industrial continuous mesh facade. This can be seen as a metaphor of the New York cityscape in general.
The expanded aluminium mesh on the facade skin wraps the entire building, softening its edges and hiding the windows throughout the day. This was meant to allow the building to melt into its surroundings and increase its sense of transparency and lightness, as well as give it a sense of blurred lines and edges. The use of aluminum panels behind the mesh also give a shallow depth and clean look to the facade.
Upon studying this detail, one of the main critiques which can be found is the fact that the facade is not actually as continuous as it is meant to appear. For example, at the corners of the building, the mesh skin does not join together, and at the bottom of the overhangs, a completely different mesh is used. Perhaps due to the budget, or because “the quality of craftsmanship in New York is known to be substandard” the building is not as detailed as it could have been in some specific areas (Ouroussoff 2007). The interior look of the mesh through the windows is also criticized, as it does not act as a true shading device, and has a very cold look to it. “Seen from outside, the strip windows there emit a blurred glow through the mesh. But from within, the metal creates a dispiritingly correctional effect: inmates look through the grate at a skyline partitioned into little diamonds” (Davidson 2001).
The most critical detail of this building is, of course, the mesh skin. However, it can also be considered as one of the main issues with the facade of the building. When looking into this detail, it can be considered that perhaps a certain change in materiality and nature may fix many of the issues noted above, while still remaining true to the nature of the building and its design concept.
The new proposed detail offers a look at the use of a metal fabric, as opposed to the expanded aluminium mesh. Metal fabric involves small strips or wires of metal which are weaved into a kind of fabric mesh. There is a wide diversity of mesh weave types, and a very wide range of colour options, allowing for expansive design possibilities and mass-customization.
For this new detail, the fabric could be made of an aluminum metal mesh fabric, with connections of the same metal, in order to relate to the aluminum side panels beneath. The mesh is quite small, so it acts as a much better light filter than the New Art Museum’s current large expanded aluminium mesh, while still allowing in a good amount of filtered incident light. The metal fabric also gives the exterior of the building a very monolithic feel, just like the current expanded mesh, but it is very transparent when viewed straight on from inside the building’s windows. This eradicates the “dispiritingly correctional effect” of the use of expanded aluminum panels over the windows, and instead allows for a very good view straight through the glass, while still hiding the interior when looking from the exterior.
The new proposed detail offers a look at the use of a metal fabric, as opposed to the expanded aluminium mesh. Metal fabric involves small strips or wires of metal which are weaved into a kind of fabric mesh. There is a wide diversity of mesh weave types, and a very wide range of colour options, allowing for expansive design possibilities and mass-customization.
For this new detail, the fabric could be made of an aluminum metal mesh fabric, with connections of the same metal, in order to relate to the aluminum side panels beneath. The mesh is quite small, so it acts as a much better light filter than the New Art Museum’s current large expanded aluminium mesh, while still allowing in a good amount of filtered incident light. The metal fabric also gives the exterior of the building a very monolithic feel, just like the current expanded mesh, but it is very transparent when viewed straight on from inside the building’s windows. This eradicates the “dispiritingly correctional effect” of the use of expanded aluminum panels over the windows, and instead allows for a very good view straight through the glass, while still hiding the interior when looking from the exterior.


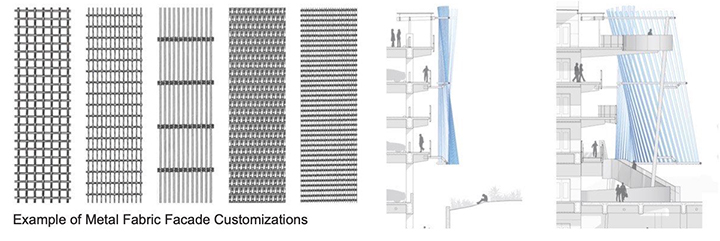
There are many benefits to using the metal fabric mesh, which, surprisingly, has not been commonly used in too many building facades, most of which are on parking garages. When it has been used, it is almost always either used like a curtain, or brought quite far away from the inner sides of the buildings, as almost a second facade or shell. For this new detail, this design is being re-fabricating as more of a skin, similar to the aluminum mesh currently on the New Art Museum, and less as a separate entity shell or curtain. Over the solid aluminum panels below, the metal fabric will create the softening of corners and play of light as more of a facade skin layer, creating the same type of clean look as the current New Art Museum. The mesh can be seen through when looked at from straight on, so the aluminum panels below this will allow the building to still remain blurred and monochrome from all directions.
The wire mesh fabric is able to be tensioned over the full height of the facade using flat tension profiles and pressure springs with tube frames and wire connections at each floor level to help with any lateral wind loads. This is a common technique for attachment of wire mesh fabric, however, this will be done in a completely continuous method, where the mesh will wrap around a metal bar at the base of the overhangs, top of the flat roofs, and all corner conditions. The tension supports and springs will then connect horizontally to the existing structure of the building. The new detail shows these connections at the base of the overhang. Instead of using metal panels which stop at the corner of the overhang, the mesh will wrap around and continue straight to the structure at the side of the overhung facade.
In order to get this detail out to others, the manufacturers of the metal fabric mesh could be contacted to use the detail as an example of a new possibility and way to fabricate this mesh for a very continuous and clean facade. The possibilities for this mesh are endless, and this is just one new detail of how it could be used, but if there is ever a building inspired by the New Art Museum that is looking to correct its mistakes, this is the detail which they could look into. The cost can also be advertised as much less than a panel cladding or a framed solution, since there is less substructure involved with the metal fabric cladding. The mesh fabric can be made of any type of metal, but the sustainability factor of using metal can also be advertised, as it is a material which is very durable, and can also be recycled and reused an indefinite amount of times without losing its qualities. The fabric mesh is also able to be integrated in sliding or hinged frames for removable solutions for shading devices which are not permanent.
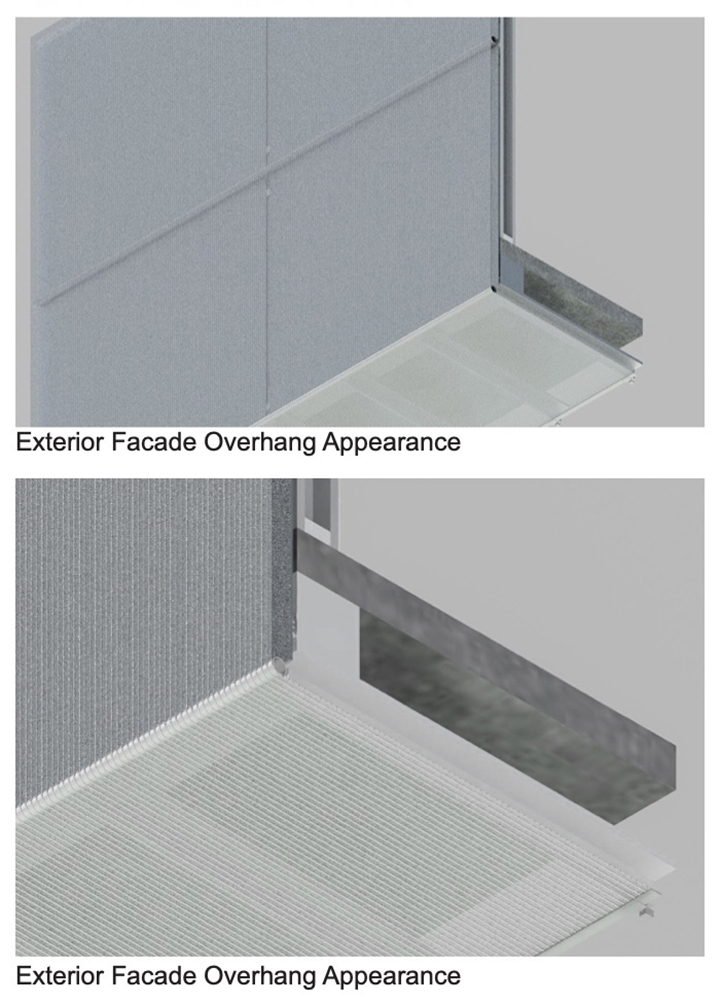

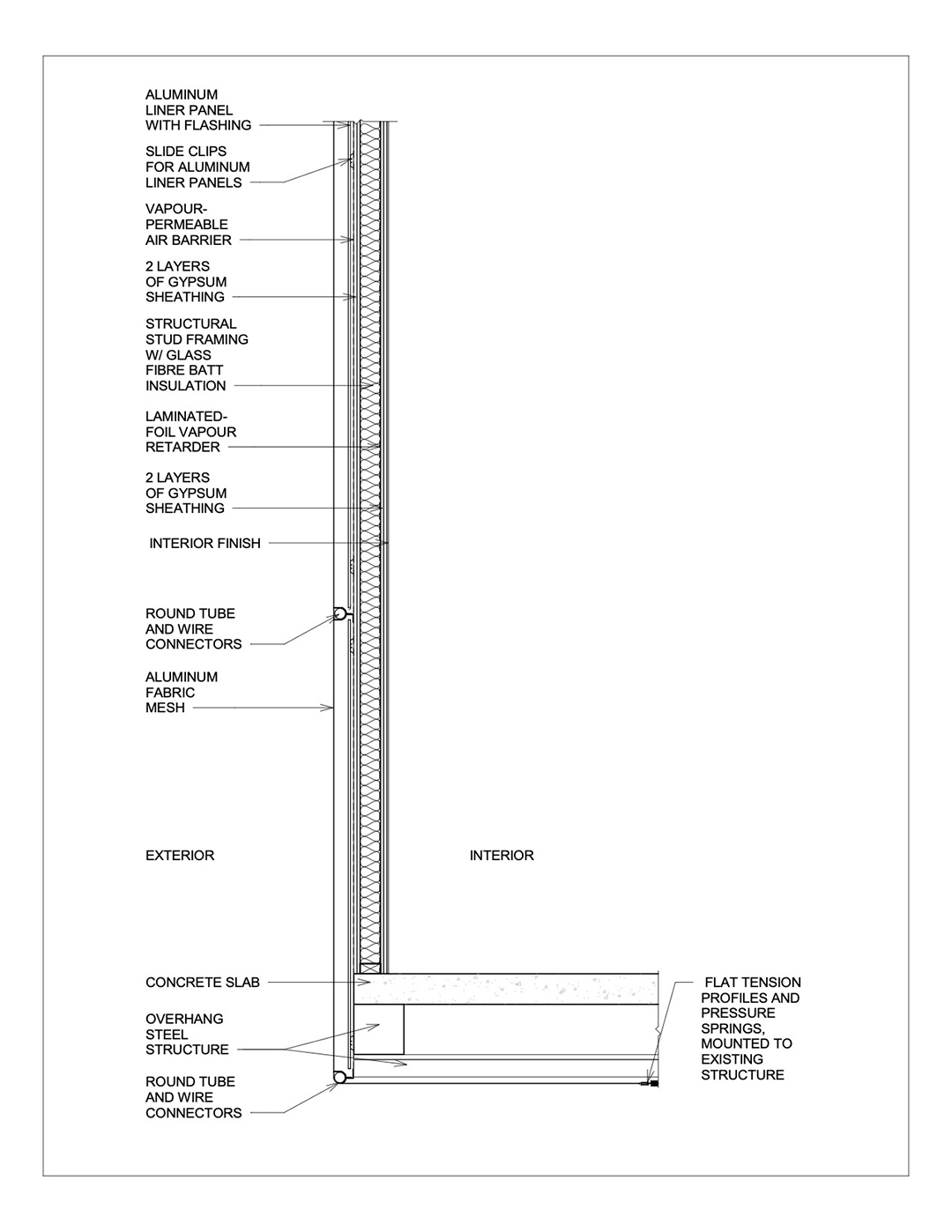
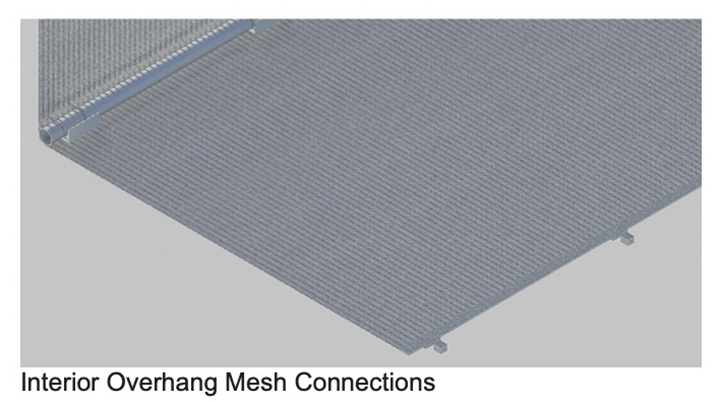
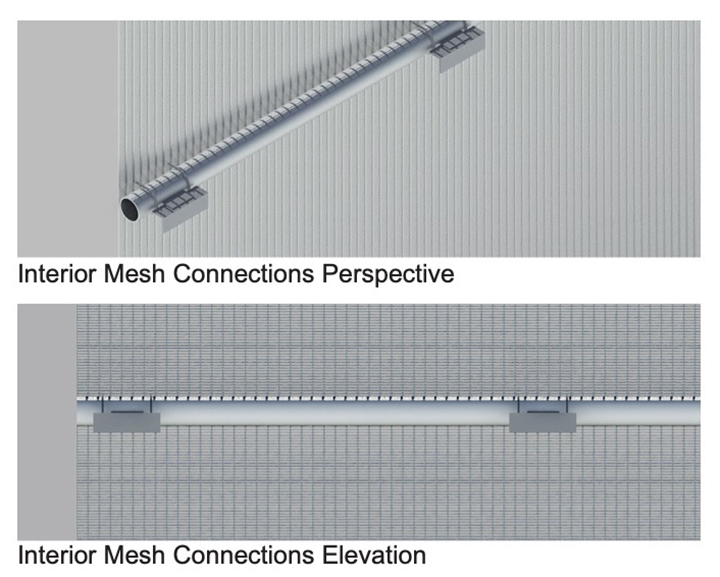
Justin Arbesman
Project 2B: Topology Optimization
Project 2B: Topology Optimization
Detail Intent
The natural world exists in resource scarcity. All forms of life have hidden optimizations within that allow for their form to exist. Bird skulls have three layers each connected with what can be called columns of microscopic bone allowing for a light yet rigid structure to not weigh the bird down. Lily Pads stem from a single root and branch out varying the thickness of their components depending on the forces acting on it. These natural optimization processes in nature beautifully tackle the organisms largest hurdles when it comes to living on this planet. We now have begun to deconstruct and reinvent these processes in the digital age. Utilizing these algorithmic processes, we can take our first principles of design and elevate them to a human designed nature. While not entirely necessary on this project by Herzog and de Meuron, the method of topology optimization is a field beginning to take over the aerospace and automotive industries and thus should be looked at in the world of architecture.
The natural world exists in resource scarcity. All forms of life have hidden optimizations within that allow for their form to exist. Bird skulls have three layers each connected with what can be called columns of microscopic bone allowing for a light yet rigid structure to not weigh the bird down. Lily Pads stem from a single root and branch out varying the thickness of their components depending on the forces acting on it. These natural optimization processes in nature beautifully tackle the organisms largest hurdles when it comes to living on this planet. We now have begun to deconstruct and reinvent these processes in the digital age. Utilizing these algorithmic processes, we can take our first principles of design and elevate them to a human designed nature. While not entirely necessary on this project by Herzog and de Meuron, the method of topology optimization is a field beginning to take over the aerospace and automotive industries and thus should be looked at in the world of architecture.
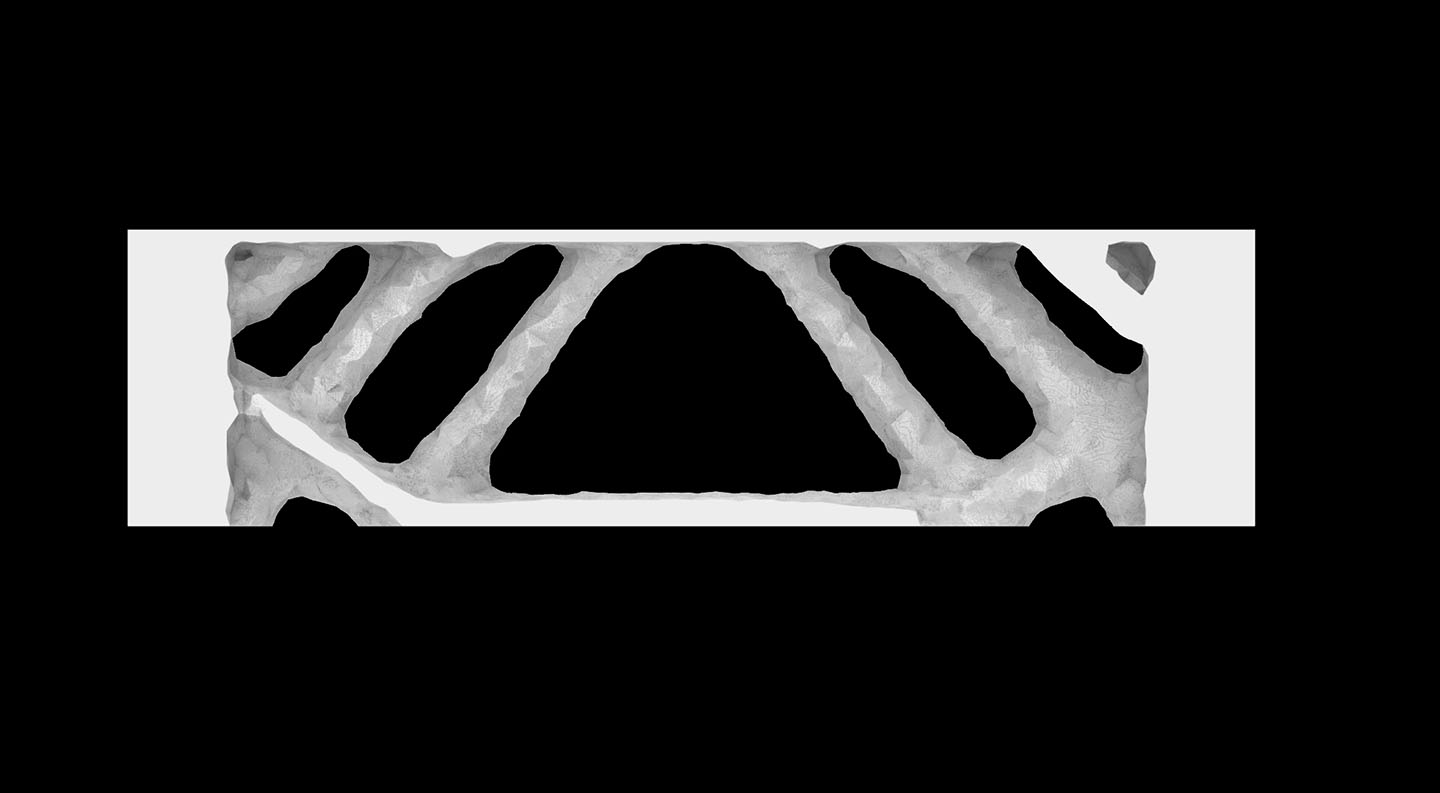
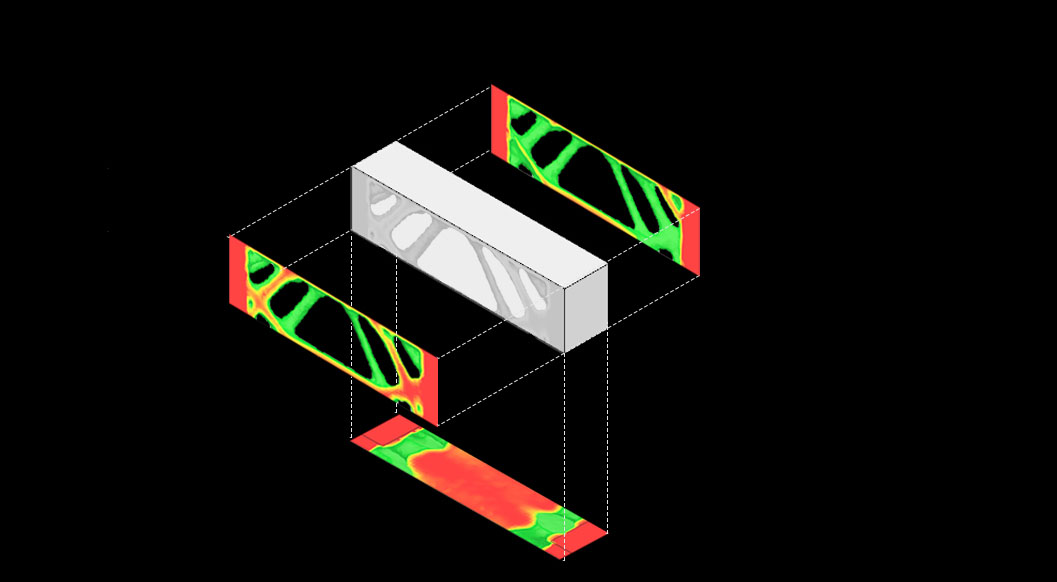
Structural engineers and architects are able to integrate the structural optimization in parallel with the standard structural calculations. Using software that is fed material properties, movement constraints, loads and load direction, the architect and engineer are able to generate force optimized forms. These forms are then further refined after the initial simulation and fed into a CAD/CAM program. With the use of a 5-axis CNC robot arm, the prefabricated components would be stripped of unnecessary material directly after the part is dimensioned. The component would then be equipped with standard heavy timber connections and used without disruption to the labor force. However, the 5-axis CNC is also capable of implementing custom complex joinery onto the part during the shaving process.
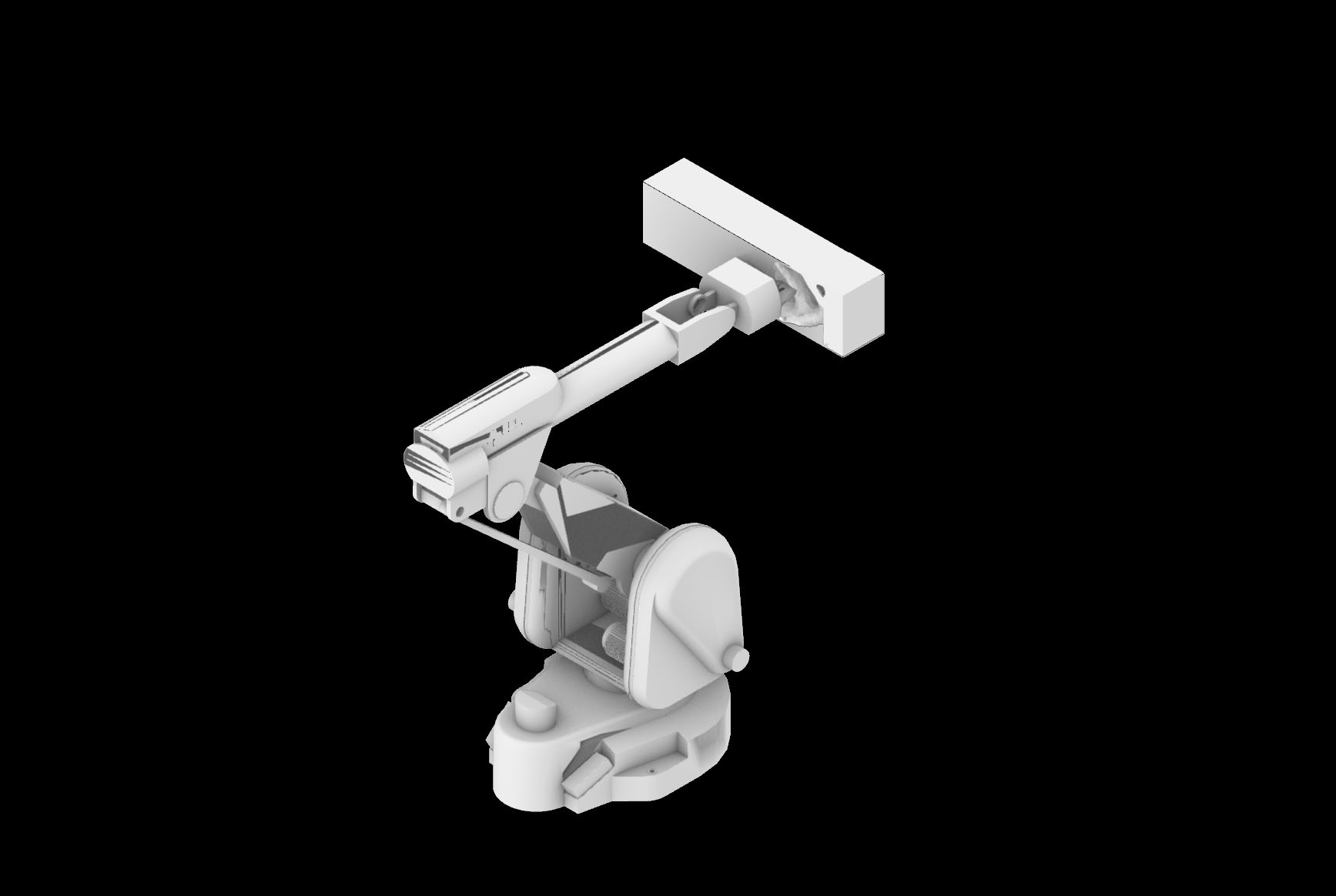
Tectonics
Then looking at a part designed using topology algorithms, even the laymen gets a feeling like nature had a role to play. The intricate, organic, and often beautiful forms that emerge give a sense of otherworldliness or of a stream of design almost unimaginable. Only through recreating processes of nature do these forms exist. Perfectly suited to its structural purposes, the optimized components visually convey the laws of nature. The results intertwine human created and naturally grown forms, a visual look into the fabric of the world. Tendrils span from one side to another, changing in size and shape showcasing the forces it counteracts. Maybe by looking at these forms more closely will we be able to further understand and conceive of structures for tomorrow.
Materiality
While topology optimization works on virtually any material, wood may be one of the best for the process. Wood has been carved, joined, spanned, bent, and cut for centuries. It is a material perfect for machining with little resistance to tools yet great overall volumetric strength. With manufacturing methods of today, any size lumber can be created by methods such as glulam allowing for large components ready for CNC milling at a staggeringly low cost in relation to its size vs raw lumber. Many professional fabrication companies are becoming custom to 5-Axis CNC milling so the topology optimization workflow can be used in unison without extra training or equipment investment.
Results
components that emerge from topology optimization have a weight reduction of around 20 - 50% depending on the material and geometry of the part. Leaving only what is necessary, offcuts can then be reused in different manufacturing processes. And due to the method of 5-axis CNC, the cost per part is only time based, the complexity has no bearing on final price outcome. These combine to have structures that can be smaller, lighter, cost roughly the same to manufacture as standard prefabricated parts, and supply derivative industries with offcuts. Topology optimization can form to any force and any load assuming the material is able to withstand it in the first place. It may be some time before methods like this are implemented but it will surely replace the crude, rigid, and often unsightly man-made structural elements of today.
While topology optimization works on virtually any material, wood may be one of the best for the process. Wood has been carved, joined, spanned, bent, and cut for centuries. It is a material perfect for machining with little resistance to tools yet great overall volumetric strength. With manufacturing methods of today, any size lumber can be created by methods such as glulam allowing for large components ready for CNC milling at a staggeringly low cost in relation to its size vs raw lumber. Many professional fabrication companies are becoming custom to 5-Axis CNC milling so the topology optimization workflow can be used in unison without extra training or equipment investment.


components that emerge from topology optimization have a weight reduction of around 20 - 50% depending on the material and geometry of the part. Leaving only what is necessary, offcuts can then be reused in different manufacturing processes. And due to the method of 5-axis CNC, the cost per part is only time based, the complexity has no bearing on final price outcome. These combine to have structures that can be smaller, lighter, cost roughly the same to manufacture as standard prefabricated parts, and supply derivative industries with offcuts. Topology optimization can form to any force and any load assuming the material is able to withstand it in the first place. It may be some time before methods like this are implemented but it will surely replace the crude, rigid, and often unsightly man-made structural elements of today.
Justin Arbesman
Material Design Innovation P2C
Material Design Innovation P2C
Topology Optimization
Recent innovations in digital fabrication, specifically related to the emerging field of 3D printed concrete formwork, has opened the doors to projects that use extremely complex geometry while having the cost of formwork be fixed to just material usage and time on a viable printing robot. This field of research has discovered the usage of automotive and industrial structural optimization software into the realm of architecture. Previously the geometries generated were only references for engineers to design optimal structural paths to save weight on parts, however in the case of concrete, a material that has the properties of both fluid and solid, the actual mesh generated from these optimization softwares can be used to create forms that have roughly 70% less material than their original unchanged volume.
Recent innovations in digital fabrication, specifically related to the emerging field of 3D printed concrete formwork, has opened the doors to projects that use extremely complex geometry while having the cost of formwork be fixed to just material usage and time on a viable printing robot. This field of research has discovered the usage of automotive and industrial structural optimization software into the realm of architecture. Previously the geometries generated were only references for engineers to design optimal structural paths to save weight on parts, however in the case of concrete, a material that has the properties of both fluid and solid, the actual mesh generated from these optimization softwares can be used to create forms that have roughly 70% less material than their original unchanged volume.
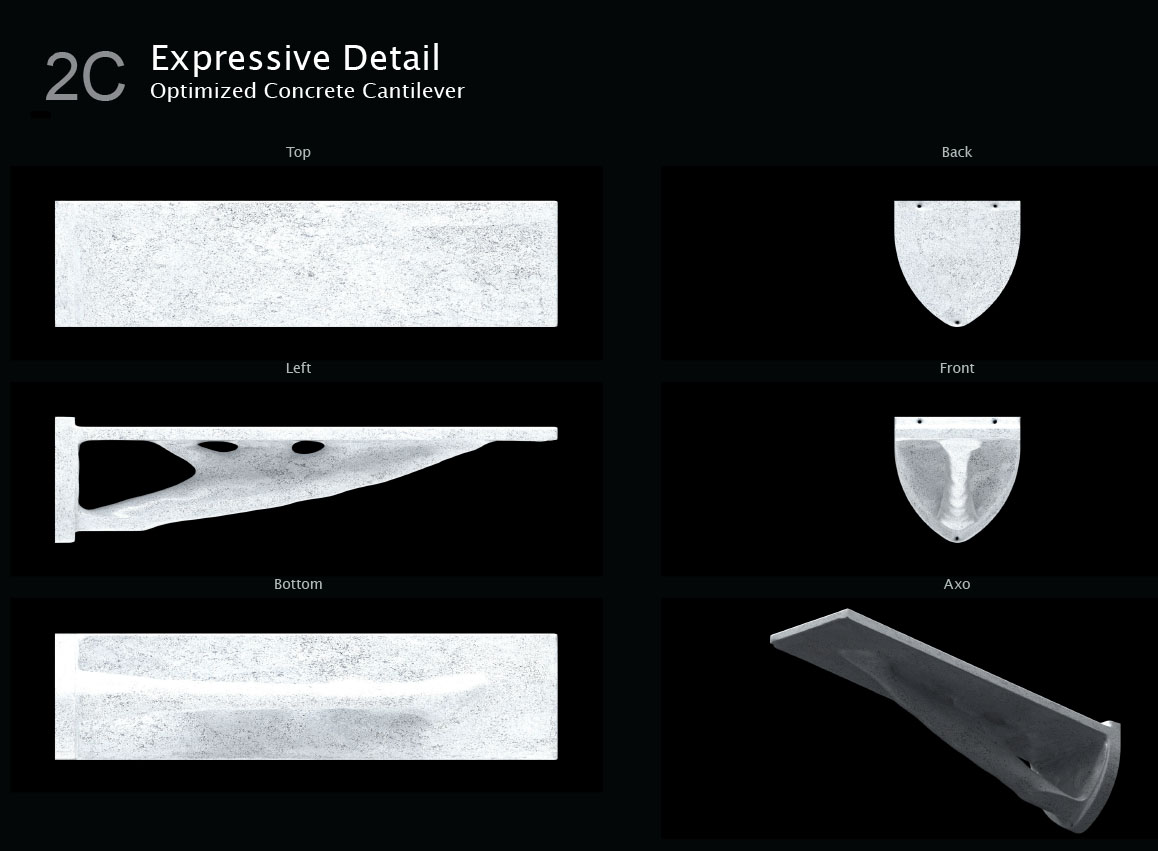
Method
As seen in projects by ETH in Zurich, the output of these softwares are inverted and converted into a mold that is then 3D printed with either plastics for repeat casting or dissolvable molds for extremely intricate components. In this detail, I generated a concrete cantilever using the topology optimization capabilities of Fusion 360 and fed the results into Rhino 7 to better manipulate the geometry. The result is a form that has both the benefit of looking at a very specific organic aesthetic while also using only 30% of the concrete needed for its shape as compared to traditional forming methods.

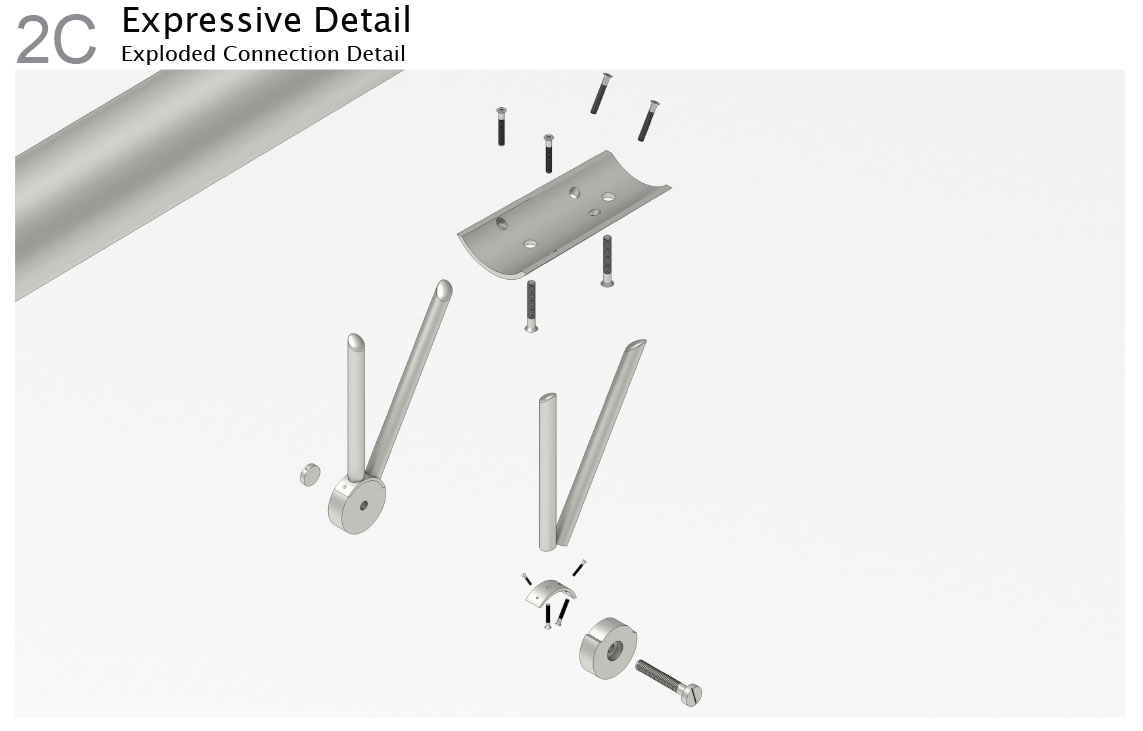
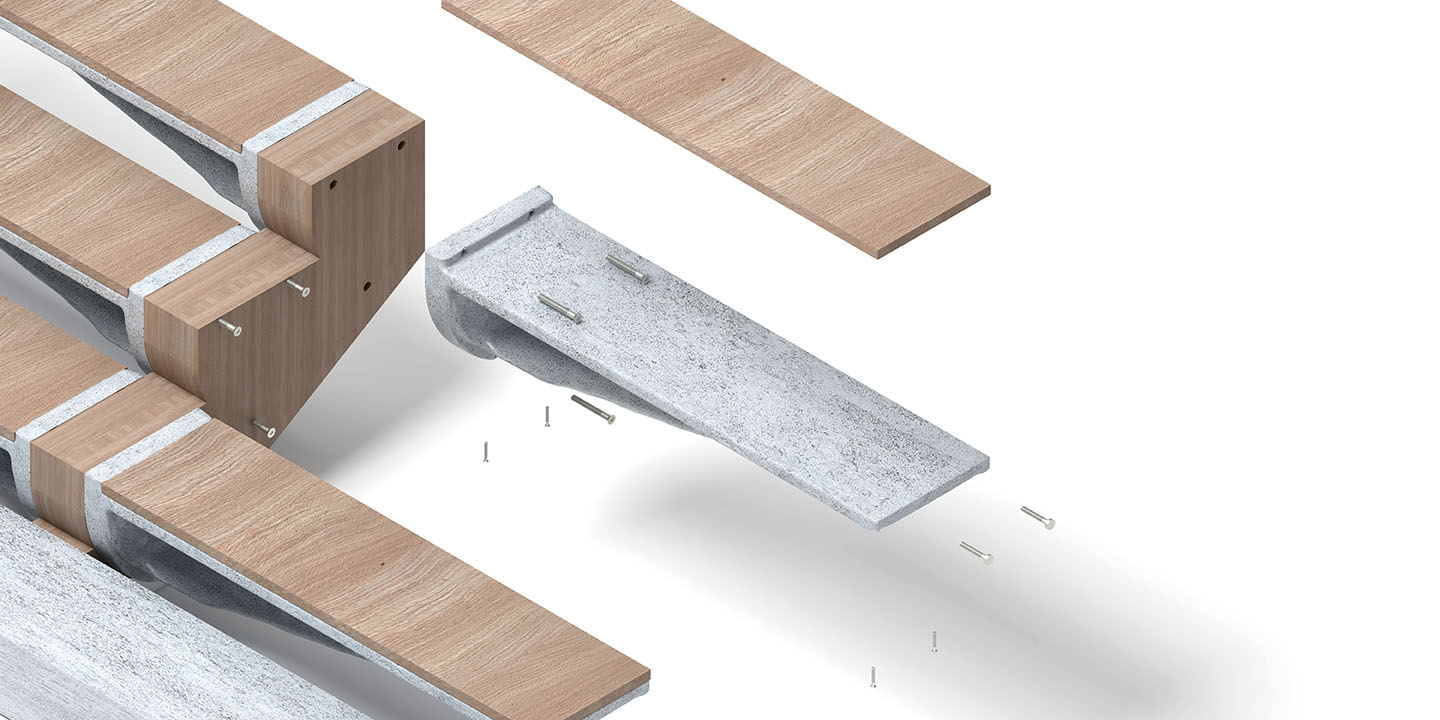
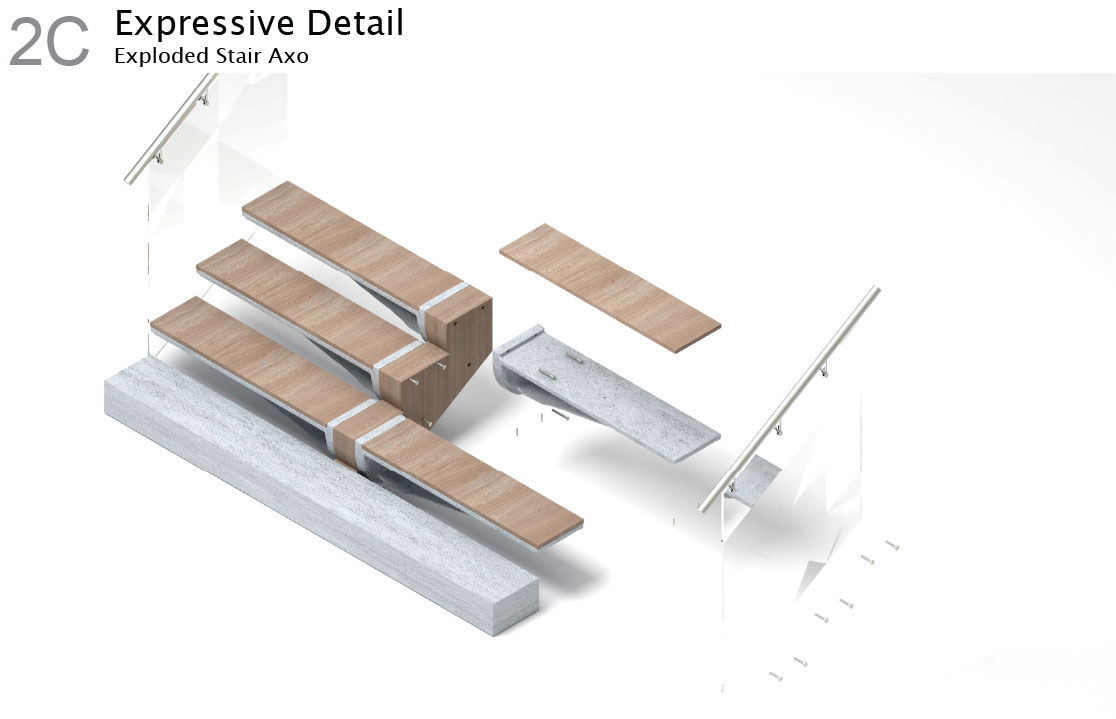
To emphasize the generated design, the pieces are bolted to a 5-ply CLT spine that runs through the whole stair. Thin wooden veneers are placed as treads to hide the mounting holes and to match the CLT spine while glass is used as the main railing support and is bolted to the edges of the concrete generated wing. The railing is held on using a minimal steel (or aluminum) connector that references the angles generated in the topology optimized concrete part. The juxtaposition of minimalism and organic geometry accentuates both and allows the stair to fit into the current aesthetic of my building while showcasing the potential projects that the digital fabrication facility is capable of creating.
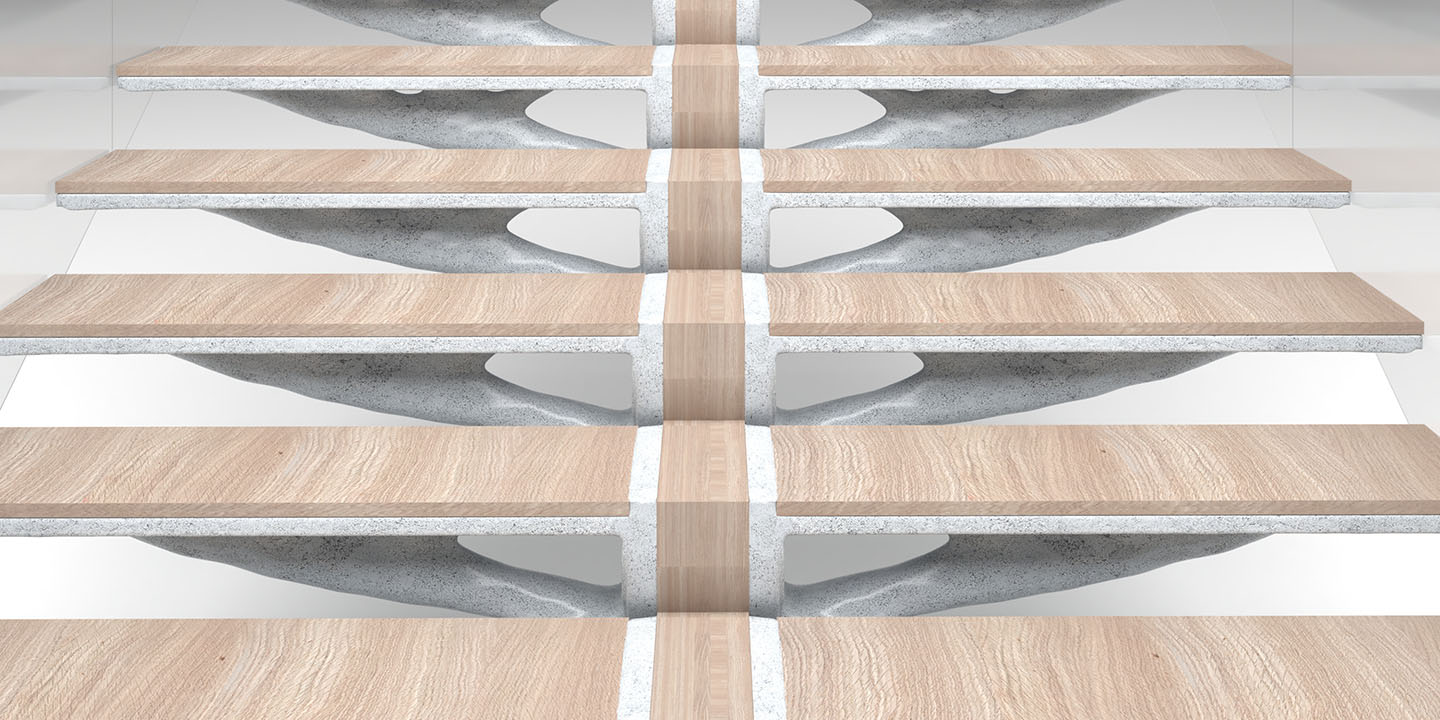
