Caitlin Chin
Project 2A - Individual Advanced Construction Tectonic and Material Study
Project 2A - Individual Advanced Construction Tectonic and Material Study
This assignment objective is to develop a deep understanding of the concept of Architecture as current and future artistic expression of tectonic materiality in an advanced constructed building, in a geographically relevant place. Students will look at the system of elements, techniques and technologies, current and as forecast and their affect on the practice of Architecture, the construction industry and sustainable futures. In addition, the project goal is to provide applied construction techniques and manufacturing in order to prepare the student for future professional engagement.
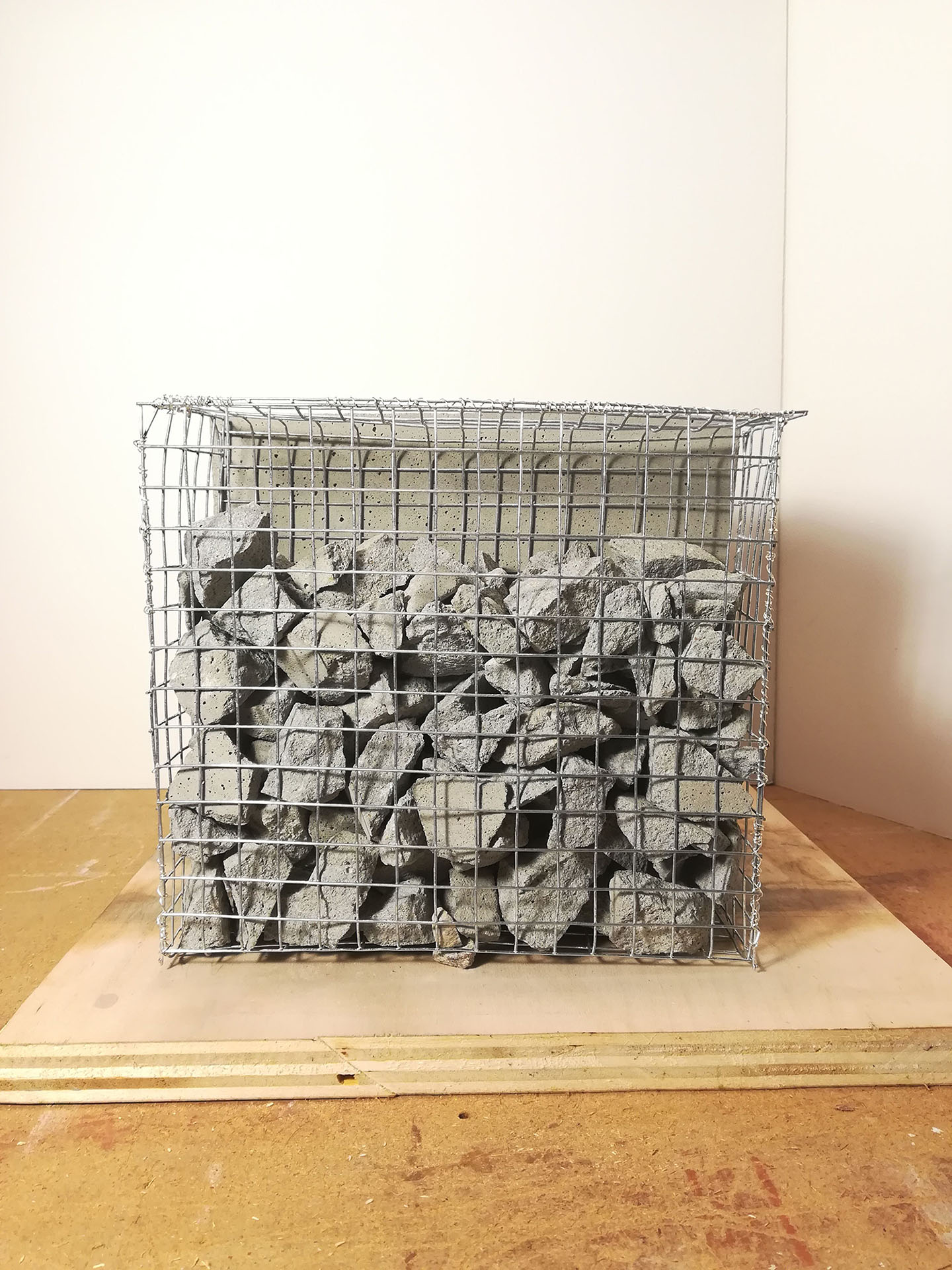
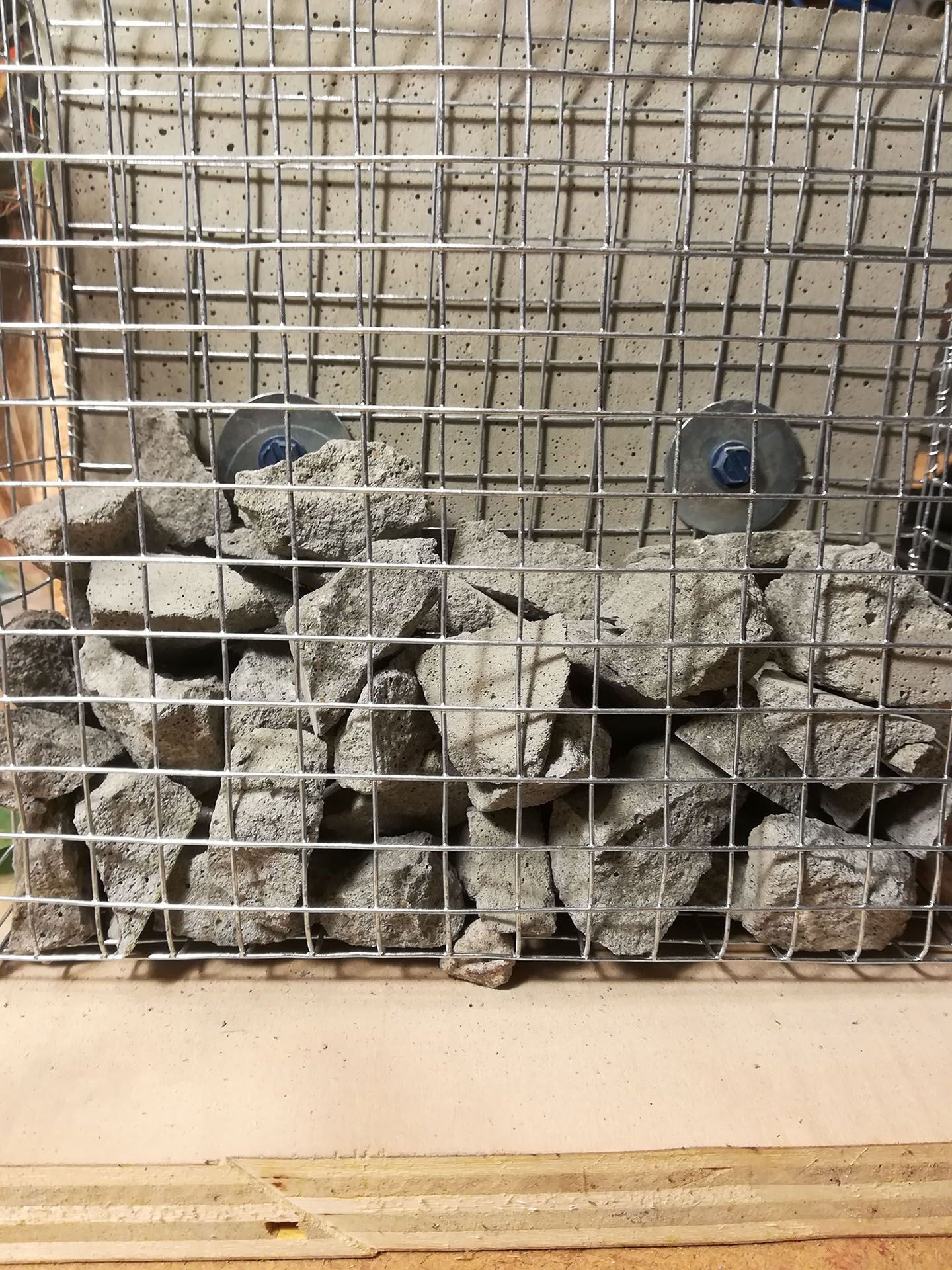
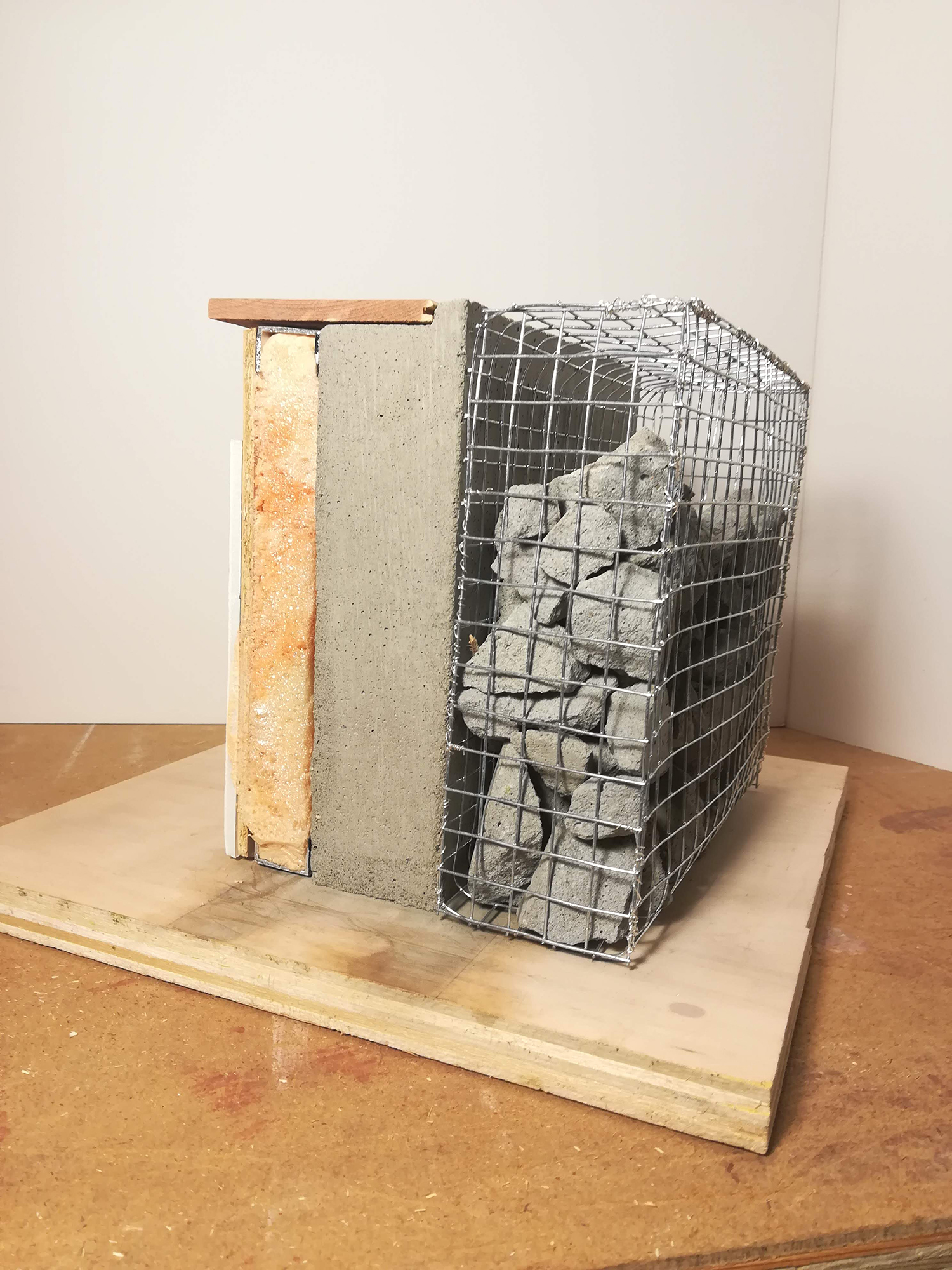

This building is a concrete building through and through. The main structure is made of reinforced concrete and the gabion cage is the exterior cladding. These gabion walls are filled with ballasts that is crushed concrete instead of stone which speaks their intention of recycling concrete. Because the gabion cage still allows rain and snow to interact directly with the structural wall, there is a sealant applied to the exterior side of the wall. Next will be the insulation, plywood and gypsum layers used for the interior finish of the wall. Douglas fir wood was also used as an accent material in this detail for the interior window frame. Their wood accents speak to their intention to reconnect with nature and their sustainable approach to concrete as the building is right beside Mt. Sobaek National Park.
How it relates to the Overall Conception:
The Hanil cement plant, the client of the Hanil Visitor Centre & Guest House, acknowledges the environmental impact of concrete as a problem. The intention of the visitor centre and guest house is to educate visitors about recycled concrete. The building itself showcases the potential of recycled concrete through different types of formwork and casting techniques in its own construction. As mentioned before the ballasts used for the gabion wall was crushed, leftover concrete of the east wall which supports their goal into looking at new ways of recycling concrete. This introduces the concept of a closed loop construction process between the waste of the east wall to be reused in the south wall. The crushed concrete was also used for the roof, interior railings in gabion cages and larger ballasts were integrated into the landscape design. The future for this interpretation of the gabion wall provides opportunity of using recycled concrete ballasts without worrying about the structural integrity of the concrete.
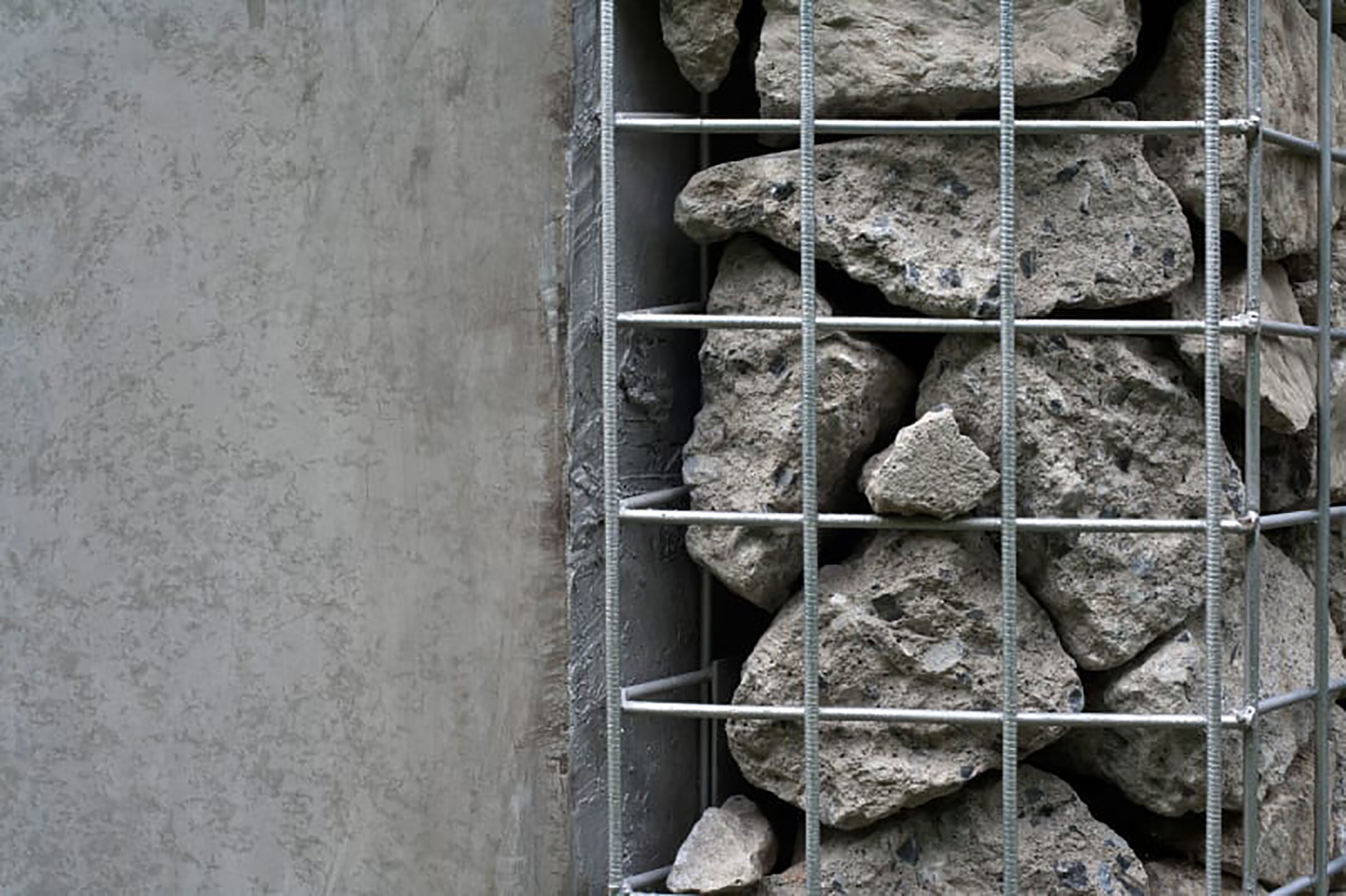
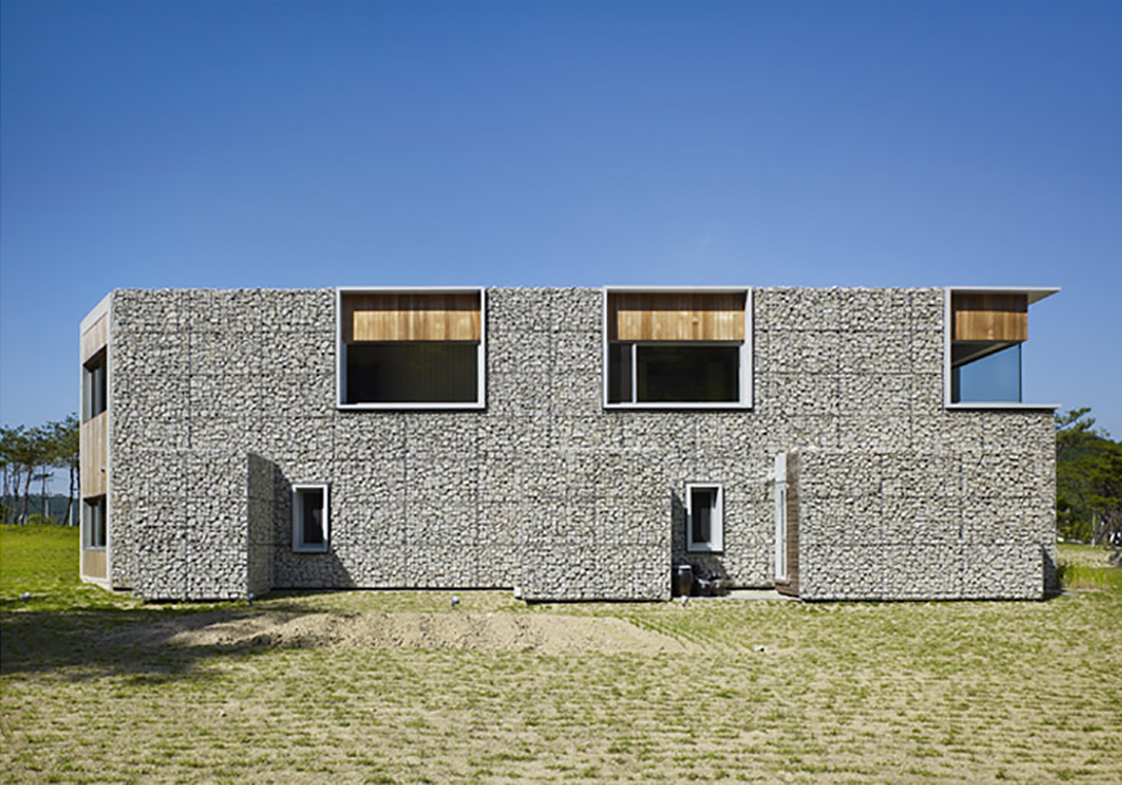
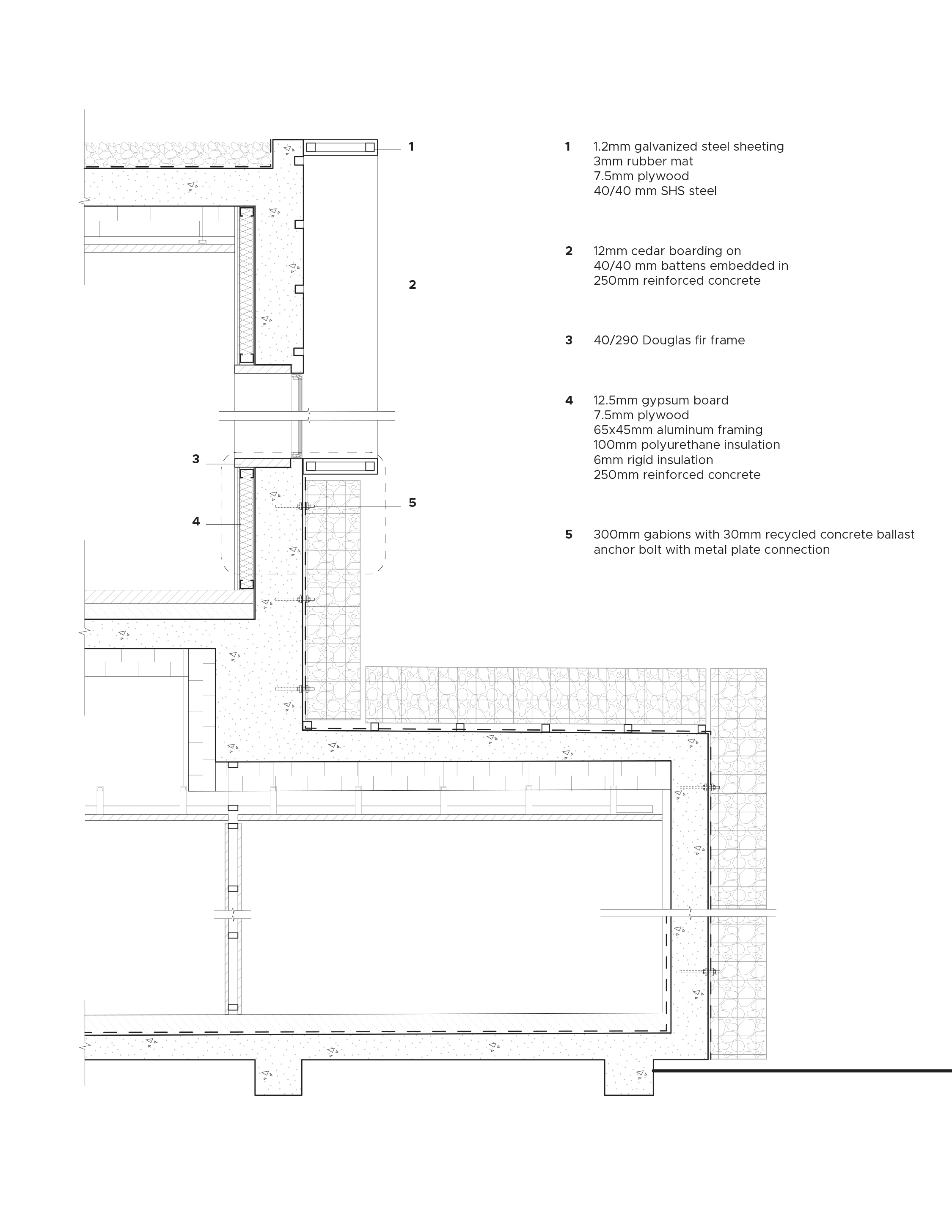
Why the Detail was Chosen:
The chosen detail is the south gabion wall of the Hanil Visitor Centre & Guest House in Korea. This wall acts as one of the main facades of the building along with the east fabric formed wall. The construction of the wall is significant because it reinterprets the typical use of a gabion wall. Traditionally, gabion walls are filled with stone and used as a retaining wall, but in this project the leftover concrete from the east wall was crushed to take the place of the stone. Therefore, the gabion wall acts more as a cladding element that is attached to the reinforced concrete wall behind it.
Caitlin Chin
Project 2B - Tectonic and Material Design, Innovation, and Entrepreneurship
Project 2B - Tectonic and Material Design, Innovation, and Entrepreneurship
The assignment objective is to develop in the students the primary ingredients of design, innovation and entrepreneurship required for the architectural and construction industries. The professional scope of the Architect is changing dramatically in the 21st century. In the future, Architect’s ideas will permeate the fabrication process in its entirety. A new relationship is being established between the Architect’s traditional responses towards advanced construction in terms of tectonics and materiality.
The Hanil Visitor Centre and Guest House
Location: 77, Pyeong-ri, Maepo-eup, Danyang-gun, Chungbuk, Korea
Architect: Byoung-soo Cho (BCHO Architects)
Client: Hanil Cement Plant
![]()
Refabrication: New Material Concept
The Hanil cement plant, the client of the Hanil Visitor Centre & Guest House, acknowledges the environmental impact of concrete as a problem. Within the visitor and guest house contains samples of different ways the Hanil Cement Plant has been experimenting with various methods of using concrete. They have the intention of coming up with new ways to use concrete in non-typical ways and combining it with other materials and methods. The south wall currently has the exterior cladding as a gabion cage wall that uses recycled concrete as ballasts. However, the construction currently in place has the cage connected flat against the solid surface of the structural reinforced concrete wall. The program of the ground floor can benefit from natural daylight. The specific detail is of the electrical room that is indicated on the plan. So instead of the gabion cage, the translucent tile that the center has been experimenting with can be an alternate cladding material to allow light to enter the interior space and to display another method of recycling concrete on the building. Also in the current detail there is no interior or exterior insulation for this space, which allows for some material experimentation.
The material alternative is an option seen on the right. The tile has the crushed concrete and then resin is poured over the ballasts. The amount of concrete within the tile and the pattern that the concrete pieces can make is all customizable. As seen on the examples on display, some tiles have the concrete emerging from the resin while in others the concrete is fully submerged. It can also have different finish qualities to the surface. It can be glossy or matte.
Location: 77, Pyeong-ri, Maepo-eup, Danyang-gun, Chungbuk, Korea
Architect: Byoung-soo Cho (BCHO Architects)
Client: Hanil Cement Plant
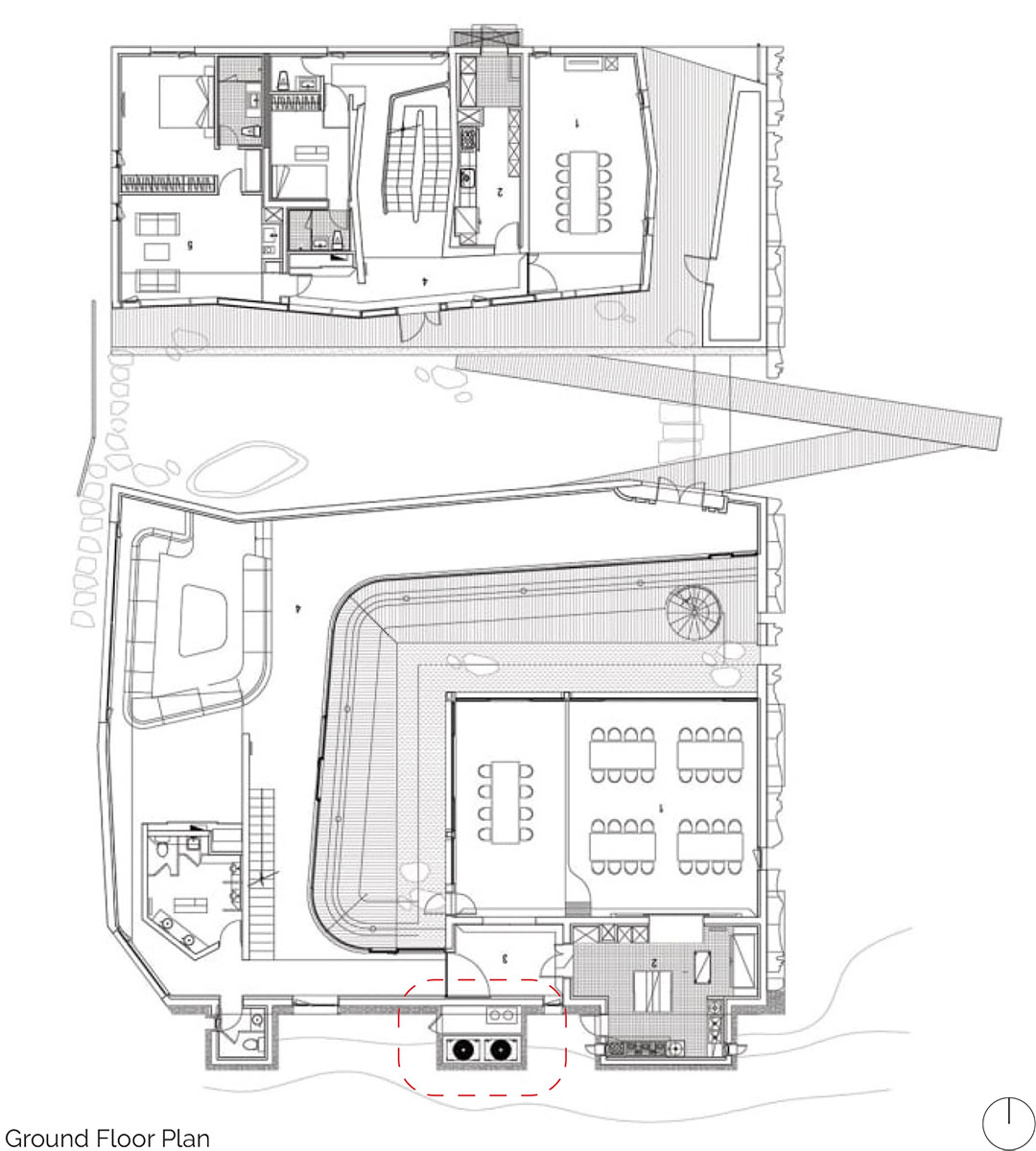
Refabrication: New Material Concept
The Hanil cement plant, the client of the Hanil Visitor Centre & Guest House, acknowledges the environmental impact of concrete as a problem. Within the visitor and guest house contains samples of different ways the Hanil Cement Plant has been experimenting with various methods of using concrete. They have the intention of coming up with new ways to use concrete in non-typical ways and combining it with other materials and methods. The south wall currently has the exterior cladding as a gabion cage wall that uses recycled concrete as ballasts. However, the construction currently in place has the cage connected flat against the solid surface of the structural reinforced concrete wall. The program of the ground floor can benefit from natural daylight. The specific detail is of the electrical room that is indicated on the plan. So instead of the gabion cage, the translucent tile that the center has been experimenting with can be an alternate cladding material to allow light to enter the interior space and to display another method of recycling concrete on the building. Also in the current detail there is no interior or exterior insulation for this space, which allows for some material experimentation.
The material alternative is an option seen on the right. The tile has the crushed concrete and then resin is poured over the ballasts. The amount of concrete within the tile and the pattern that the concrete pieces can make is all customizable. As seen on the examples on display, some tiles have the concrete emerging from the resin while in others the concrete is fully submerged. It can also have different finish qualities to the surface. It can be glossy or matte.
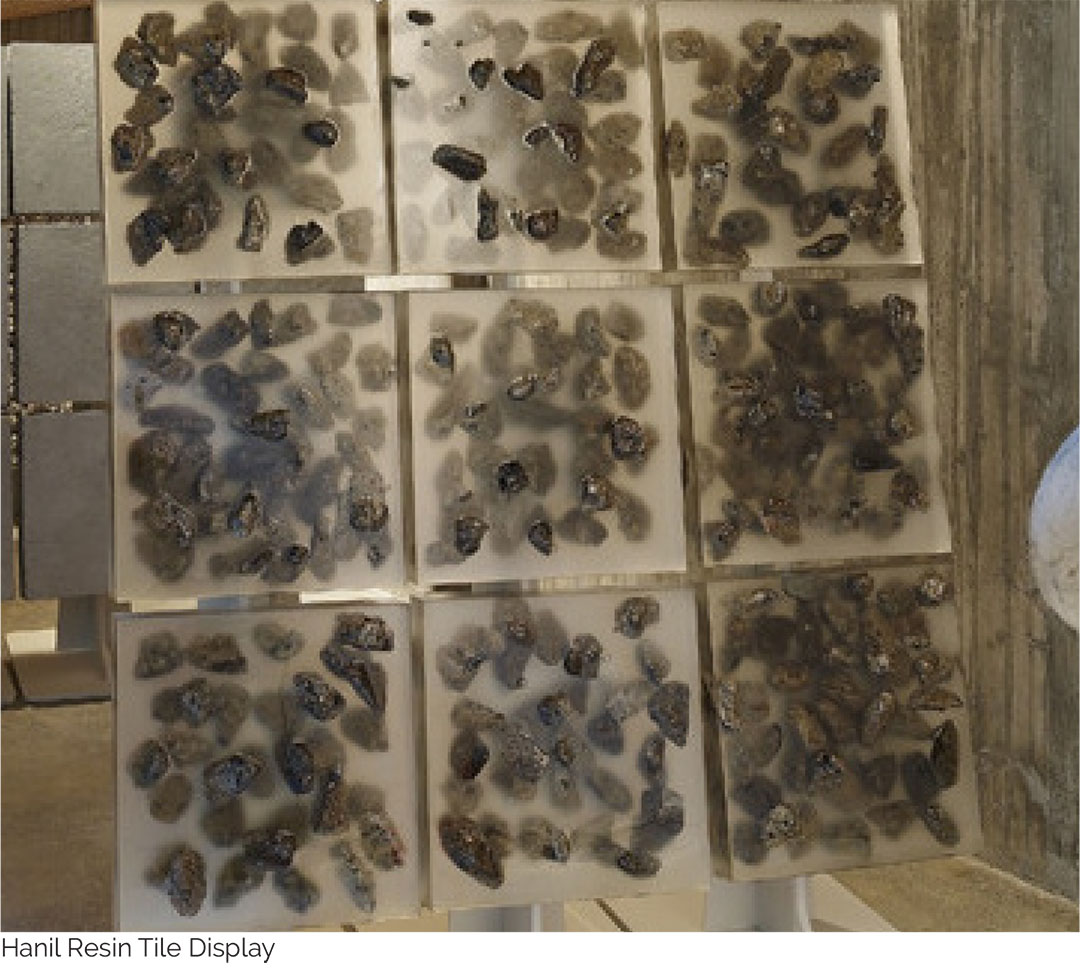
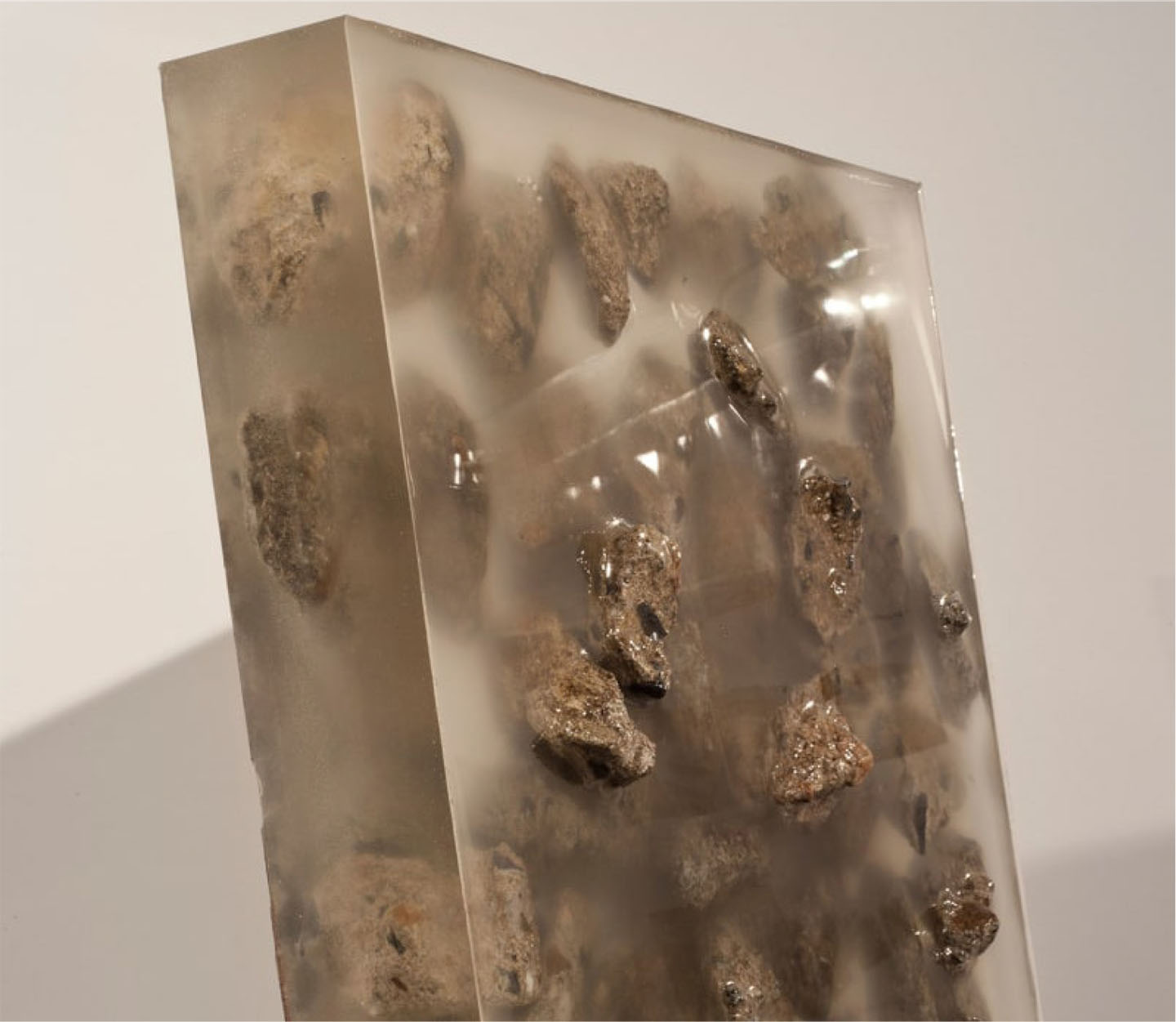
Resin Material Properties:
Casting resin is specifically designed to be casted into molds, forms, and figures. The two components of casting resin that makes it an interesting material is the low-viscosity and the ability to harden over time. Because of these properties casting resin can be used for projects that require a thicker application/ depth. Casting resin differs from epoxy resin. Epoxy resin is more viscous, has a faster curing time but can only be applied to projects with a maximum depth of 2cm (Resin Expert, 2020).
Looking into specific products for casting resin is a thermosetting resin, specifically made from polyethylene terephthalate. It is highly transparent and stiff, and it has excellent gas barrier properties. Some example of products that are made from this material is insulation, and high-performance optical films (Daido Chemical Corporation).
When in the process of casting, formwork needs to be considered. It is recommended to use silicone molds to allow for a smooth finish but also allows for easy removal of the mold. The first step would be to have a thin layer of resin in the mold to begin with and then to add the desired amount and pattern of the recycled concrete pieces. Next, additional casting resin will be poured over concrete pieces and to reach the desired thickness. It is recommended to dry for 24 hours but it also varies based on the thickness of the piece casted.
I am looking at the thin resin tiles that the Hanil Cement Plant has experimented with and making it into something that is thicker, and block like. I will be looking at glass blocks and their construction methods of wall construction for the proposed resin blocks.
Glass Block History:
The invention of glass has made a huge impact on the building industry as it allows natural daylight and views to be accessible from the interior of the building. The use of glass blocks has been reinvented over the years as it has varied in use as an interior or exterior element in the form of walls, ceilings, and floors. Glass blocks have been important in the interior architectural design to illuminate adjacent rooms and hallways mainly. The glass can be manufactured to provide the desired degree of visibility to allow for privacy and light permeability. In the exterior context, glass blocks maximize natural light to reduce energy required for artificial lighting (Architectural Products and Services, 2018).
In 1907, Deutsche Luxfer-Prismen-Gesellschaft patented the glass block strengthening process where the two pieces of glass are joined but the centre is hollow. The “air gap” within enhances the insulating qualities that glass blocks and helps with sound deadening, and fireproofing. In present day context, the pattern, texture degree of transparency and size can all be customized for any project. Additionally, over the years different mortars and silicones have been improving to join the glass blocks together (Architectural Products and Services, 2018).
I am hoping to explore and treat the resin concrete blocks similarly to the glass block construction. I will be referring to different modern examples that used glass blocks in an innovative way and looking at different details that I can learn from for the resin concrete blocks.
![]()
The invention of glass has made a huge impact on the building industry as it allows natural daylight and views to be accessible from the interior of the building. The use of glass blocks has been reinvented over the years as it has varied in use as an interior or exterior element in the form of walls, ceilings, and floors. Glass blocks have been important in the interior architectural design to illuminate adjacent rooms and hallways mainly. The glass can be manufactured to provide the desired degree of visibility to allow for privacy and light permeability. In the exterior context, glass blocks maximize natural light to reduce energy required for artificial lighting (Architectural Products and Services, 2018).
In 1907, Deutsche Luxfer-Prismen-Gesellschaft patented the glass block strengthening process where the two pieces of glass are joined but the centre is hollow. The “air gap” within enhances the insulating qualities that glass blocks and helps with sound deadening, and fireproofing. In present day context, the pattern, texture degree of transparency and size can all be customized for any project. Additionally, over the years different mortars and silicones have been improving to join the glass blocks together (Architectural Products and Services, 2018).
I am hoping to explore and treat the resin concrete blocks similarly to the glass block construction. I will be referring to different modern examples that used glass blocks in an innovative way and looking at different details that I can learn from for the resin concrete blocks.
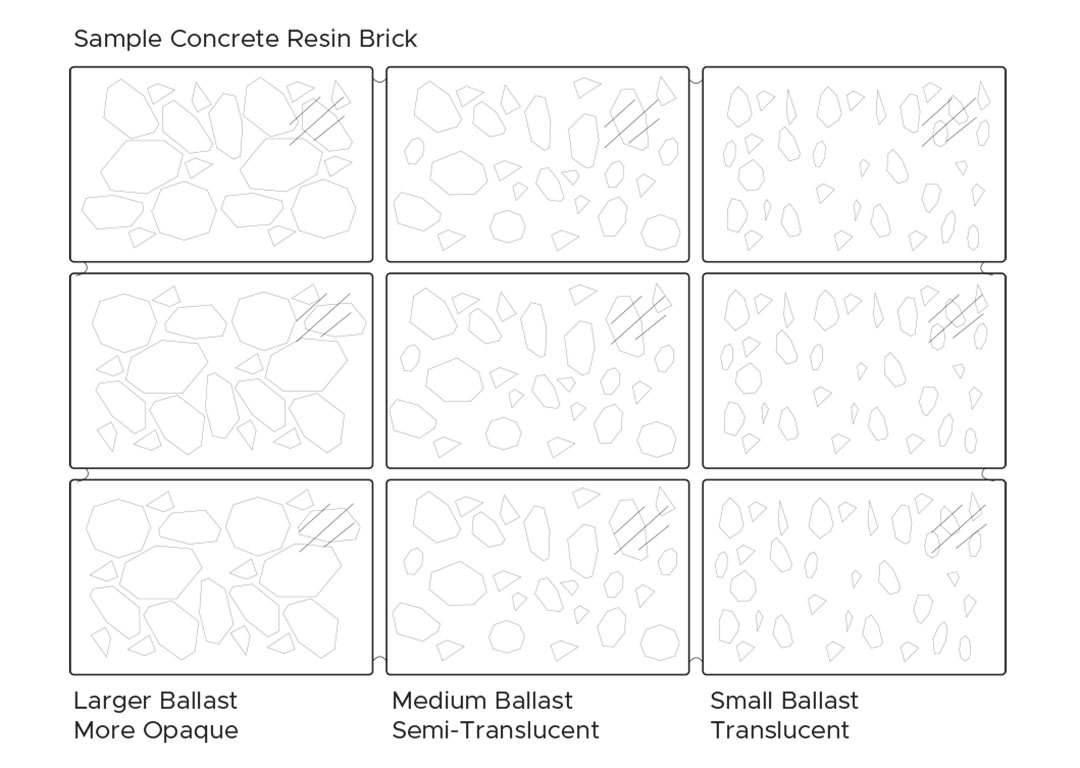

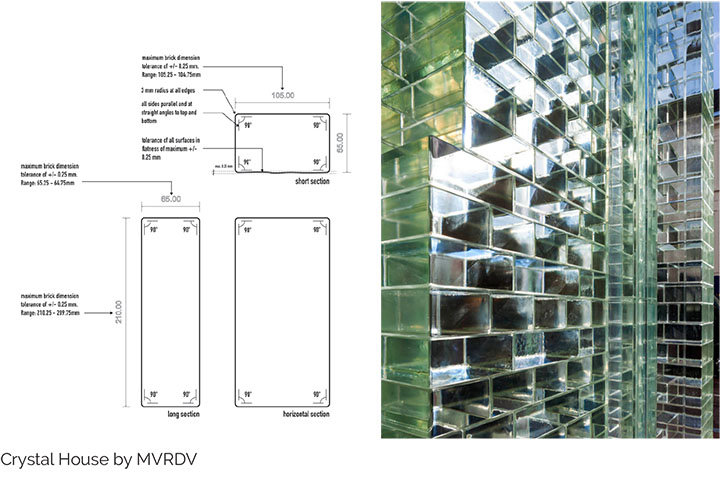
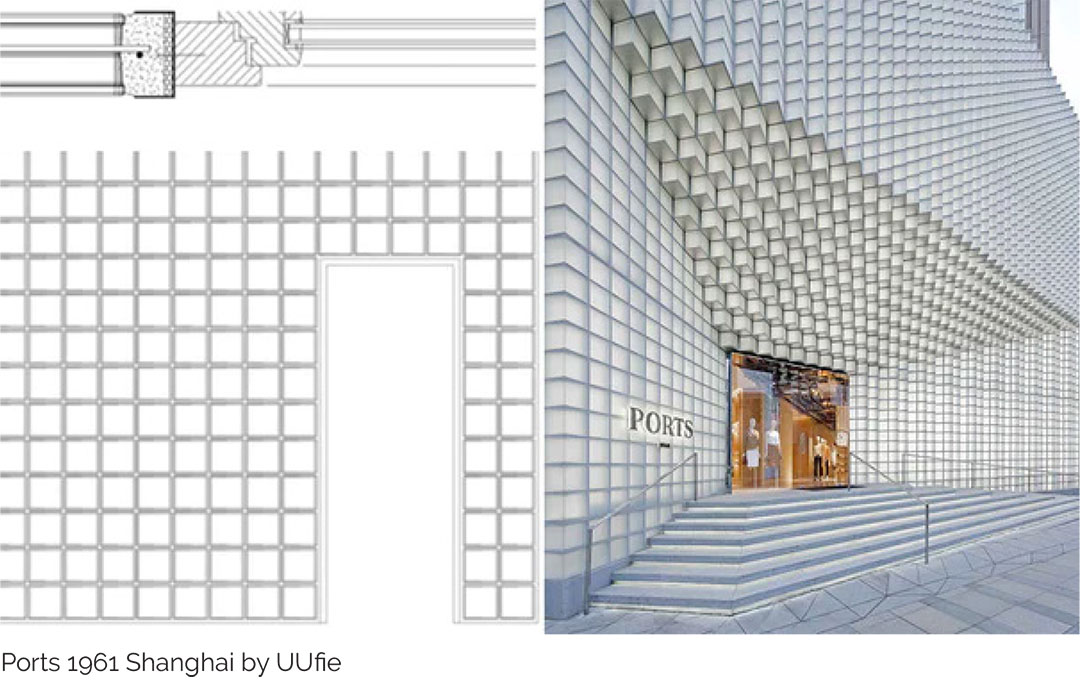
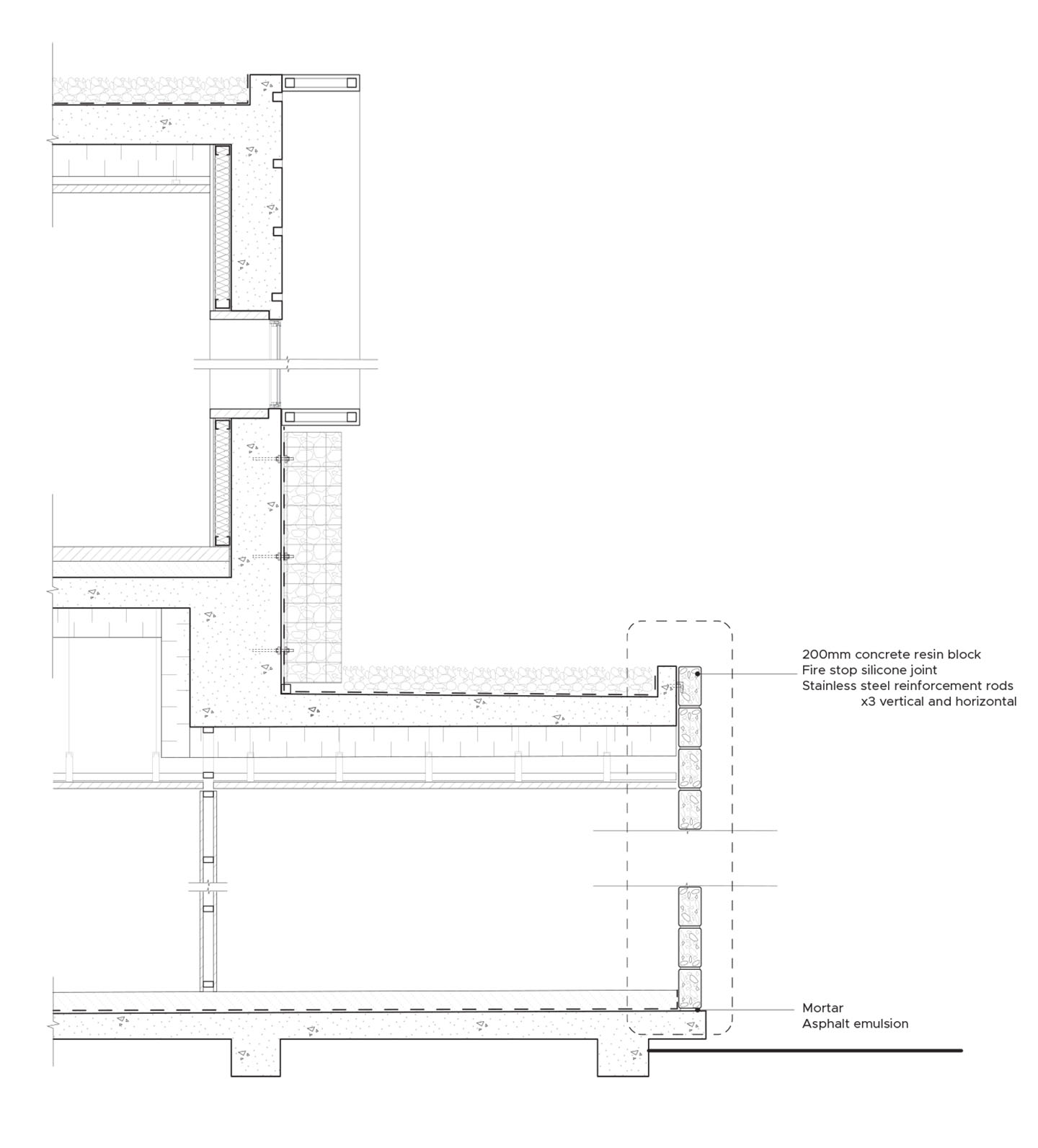