THIRD YEAR UNDERGRADUATE
Silvana Di Meglio—Hanscomb Award
![]()
Silvana Di Meglio—Hanscomb Award

About the Award
For the student with the best average in ASC 522 and ASC 622.
The following images are exemplified of work done in ASC 522 Project Economics and ASC622 Construction Documentation.
ASC 522 allowed for students to engage with different drivers of design through the Data Driven Design Project. This includes construction cost, and energy efficiency in a building, therefore, we were required to develop an understanding of how these factors are affected by massing and material choices. This project required analyses and refinement of massing designs from the studio class, to reduce capital cost and improve energy performance (decreased lifetime energy cost).
ASC 622 mainly involved group work between students, gaining knowledge on the industry. With this project being a group initiative, I would like to acknowledge my partners in collaboration: Emma Chudoba, Stephanie Vo, Tyler Chui and Hajara Hameed. The set of construction documents involves an understanding of the industry as well as the numerous different systems within construction documentation. This project added to my skills in group work and coordinating a BIM model in Revit, therefore continuously updating the BIM model and communicating to partners.
Energy Massing Model 1
The first proposed massing uses a large portion of curtain wall glazing on both exterior facades of the building. The north and south side floor to ceiling glazing allows for maximum amount of natural lighting and heating for the structure. The west and east facades are built using an exterior brick with metal studs. The materials used for this massing resulted in a total life cycle cost of $1,482,624.53. Due to the amount of glazing, seen in the cost and fuel bar graph, the costs result to be very high in the winter months because of the window wall ratio. Although the exterior glazing provides immense daylight, they result in expensive energy cost and envelope cost.
Energy Massing Model 2
In the second massing, the form is very similar however, the amount of glazing used and floor heights were reduced. In comparison to the first massing, the life cycle cost this proposed structure saves $205,051.40 for the overall life cycle cost that resulted in the significant reduction in energy expenses. Hence, the resulting life cycle cost for this massing is $1,277, 573.14. The use of brick is increased significantly as the north and south facades are using smaller window types. In addition, each floor was reduced half a meter (while still being to code) to result in smaller volumes, therefore taking the HVAC systems less energy to heat or cool a space. Overall, the decreased use of glazing and the window placing significantly impacted the price and energy for the building.
For the student with the best average in ASC 522 and ASC 622.
The following images are exemplified of work done in ASC 522 Project Economics and ASC622 Construction Documentation.
ASC 522 allowed for students to engage with different drivers of design through the Data Driven Design Project. This includes construction cost, and energy efficiency in a building, therefore, we were required to develop an understanding of how these factors are affected by massing and material choices. This project required analyses and refinement of massing designs from the studio class, to reduce capital cost and improve energy performance (decreased lifetime energy cost).
ASC 622 mainly involved group work between students, gaining knowledge on the industry. With this project being a group initiative, I would like to acknowledge my partners in collaboration: Emma Chudoba, Stephanie Vo, Tyler Chui and Hajara Hameed. The set of construction documents involves an understanding of the industry as well as the numerous different systems within construction documentation. This project added to my skills in group work and coordinating a BIM model in Revit, therefore continuously updating the BIM model and communicating to partners.
Energy Massing Model 1
The first proposed massing uses a large portion of curtain wall glazing on both exterior facades of the building. The north and south side floor to ceiling glazing allows for maximum amount of natural lighting and heating for the structure. The west and east facades are built using an exterior brick with metal studs. The materials used for this massing resulted in a total life cycle cost of $1,482,624.53. Due to the amount of glazing, seen in the cost and fuel bar graph, the costs result to be very high in the winter months because of the window wall ratio. Although the exterior glazing provides immense daylight, they result in expensive energy cost and envelope cost.
Energy Massing Model 2
In the second massing, the form is very similar however, the amount of glazing used and floor heights were reduced. In comparison to the first massing, the life cycle cost this proposed structure saves $205,051.40 for the overall life cycle cost that resulted in the significant reduction in energy expenses. Hence, the resulting life cycle cost for this massing is $1,277, 573.14. The use of brick is increased significantly as the north and south facades are using smaller window types. In addition, each floor was reduced half a meter (while still being to code) to result in smaller volumes, therefore taking the HVAC systems less energy to heat or cool a space. Overall, the decreased use of glazing and the window placing significantly impacted the price and energy for the building.

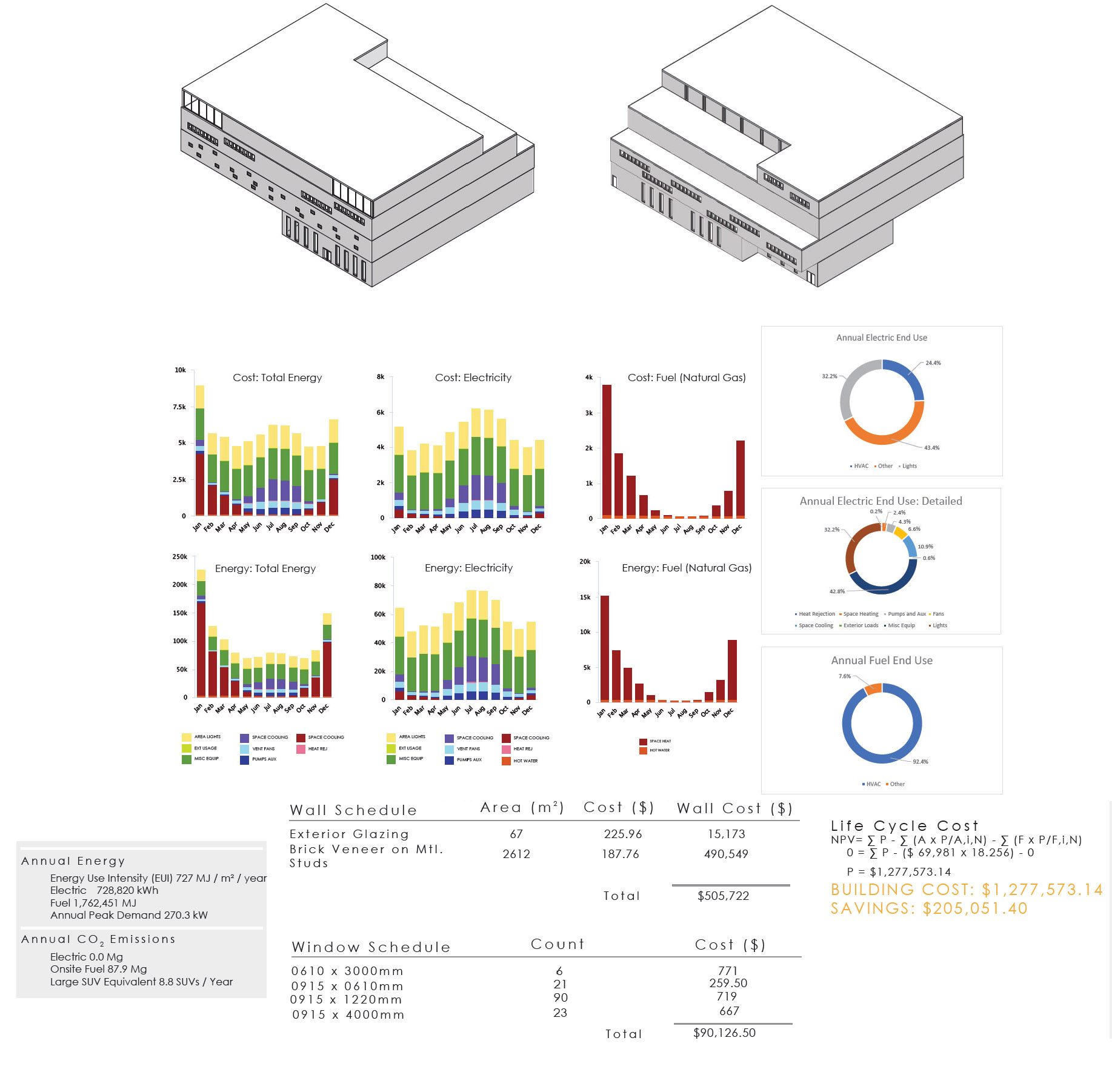
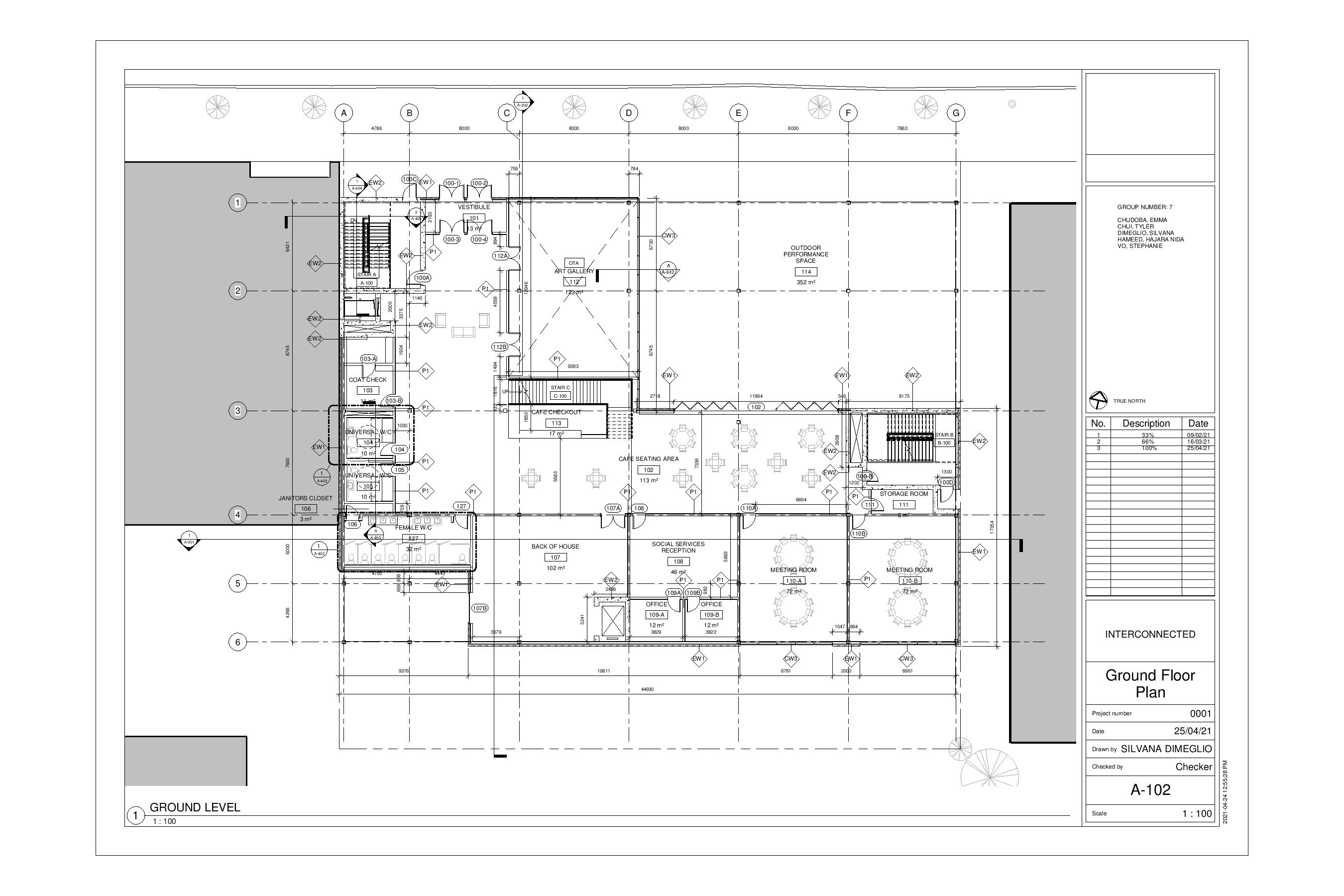

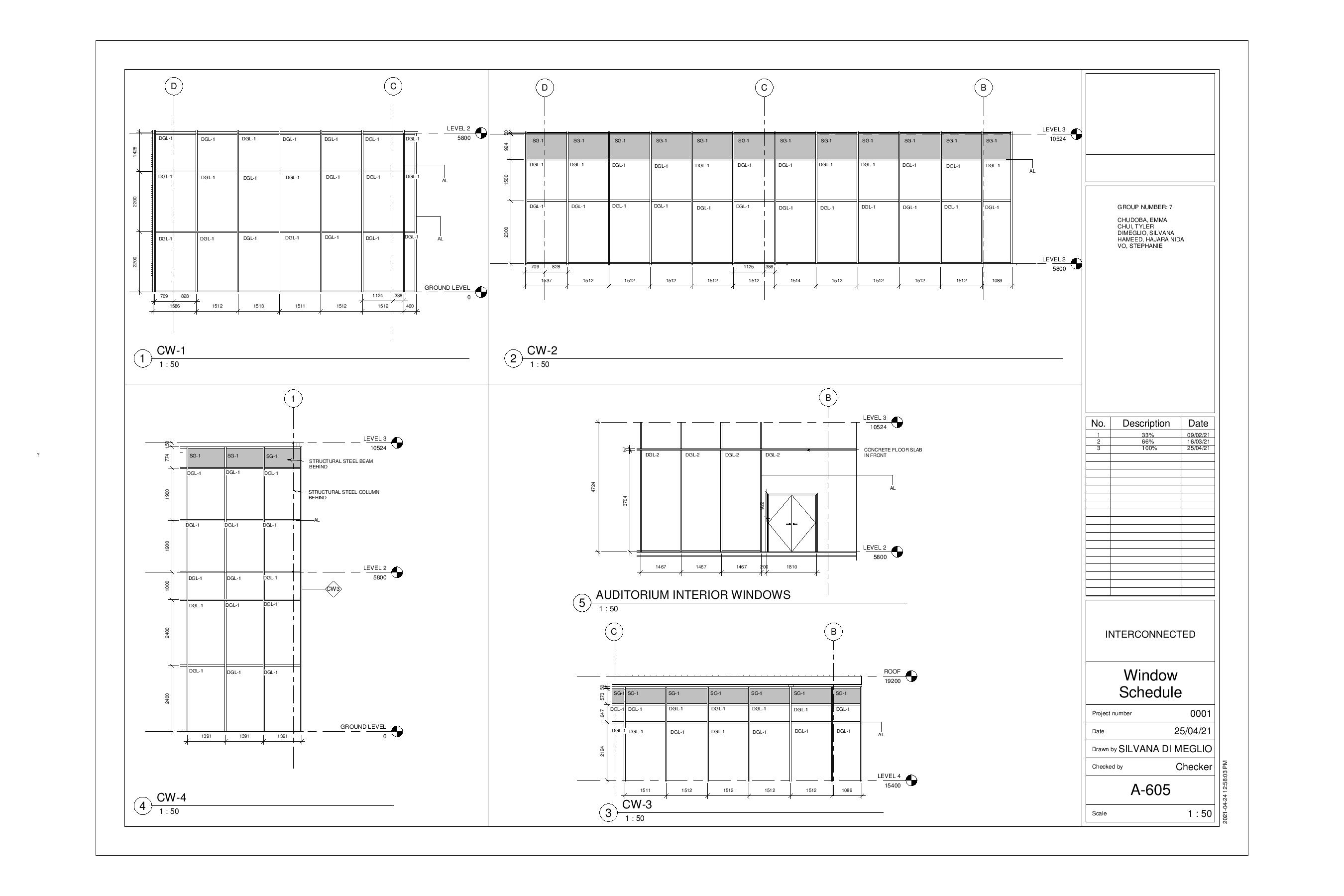
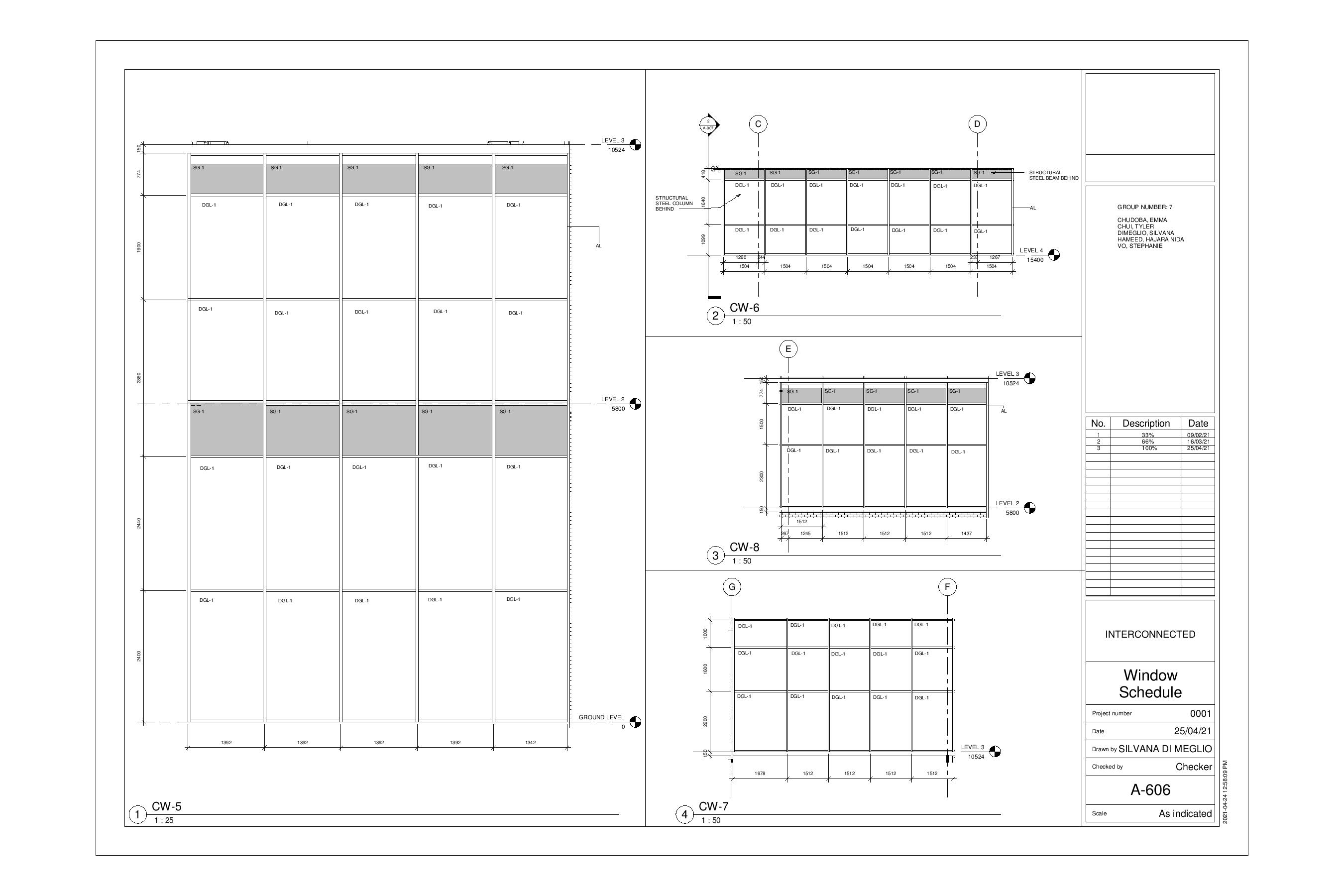